PROZESSANALYSE
Prozesskontrolle in der Zellstoff- und Papierproduktion
Bei der Zellstoffproduktion kommen neben zahlreichen Chemikalien erhebliche Mengen Natronlauge und Chlordioxid zum Einsatz.
Die zur Prozesskontrolle verwendeten pH-Sensoren unterliegen bei kontinuierlichem Kontakt zu den ätzenden Chemikalien hohen Belastungen.
Zusätzlich werden die Standzeiten der Sensoren durch den hohen Faser- und Schwebstoffgehalt der Prozessmedien limitiert, der nach kurzer Zeit starke Ablagerungen und Verkrustungen an den Messelektroden bildet.
Das raue, durch aggressive Chemikalien und einen hohen Verunreinigungsgrad geprägte Prozessumfeld erfordert Messstellen, die einen schnellen und unkomplizierten Austausch der Sensoren mit minimalem Zeitaufwand ermöglichen.
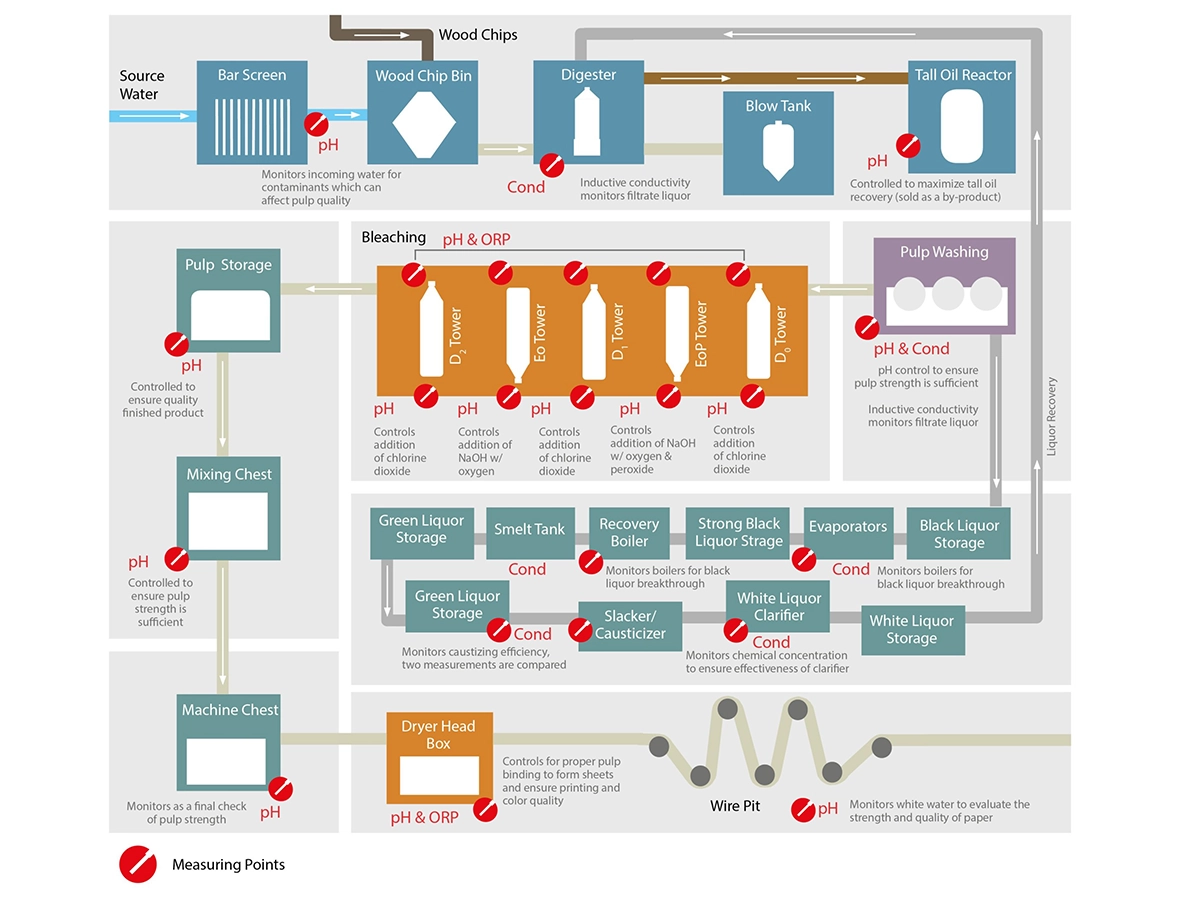
Messsensoren für die Prozesskontrolle in der Zellstoff- und Papierproduktion
Darum geht es bei der Zellstoffgewinnung
Seit der Erfindungen des Holzschliffpapiers sowie der sogenannten Sulfat- und Sulfitverfahren in der Mitte des 19. Jahrhunderts ist es ermöglich, Papier auf Grundlage von Holz zu produzieren. Bei den Sulfat- und Sulfitverfahren wird mechanisch zerfasertes Holz durch Kochen in Natronlauge und Natriumsulfid- bzw. Schwefeldioxid-haltigen Lösungen chemisch aufgeschlossen, um die enthaltenen Zellulosefasern von unerwünschten Bestandteilen zu lösen. Dazu zählen besonders die holzbildenden Lignine, „Hermizellulosen“ genannte Polysaccharide sowie Harze und Mineralien. Während die Zellulosefasern in Form wässriger Lösungen in verschiedenen mehrstufigen Anschlussverfahren gereinigt und gebleicht werden, dienen die abgeschiedenen Harze der Herstellung von Tallöl, das nach seiner Raffinierung unter anderem in der Herstellung von Seifen und Lacken Anwendung findet.
Abläufe der Zellstoffgewinnung und Papierproduktion
Neben den grundlegenden Rohstoffeigenschaften spielt die Güte der vielfältigen Reinigungs- und Mischverfahren, die der Faserstoff bei der Verarbeitung durchläuft, eine erhebliche Rolle für die Produktqualität. Dazu zählen im Wesentlichen die beim Sulfatverfahren angewendete Zellstoffkochung in der „Weißlauge“, die anschließende Filtrierung und Wäsche des Kochguts in Filterstraßen sowie die mehrstufige Turmbleichung, bei der der Zellstoff abwechselnd mit verschiedenen Oxidantien behandelt wird.
Anschließend gelangt der als „Stoff“ bezeichnete Faserbrei in die „Stoffaufbereitung“. Dort wird er zunächst in der Mischbütte mit verschiedenen Faserstoffen rezeptabhängig vermengt, gemahlen und Füllstoffe wie Kaolin, Calciumcarbonat, Leim und Farben zugegeben, um die gewünschten Eigenschaften des späteren Papiers zu erzielen. Im „Stoffauflauf“ wird der Faserstoff von Düsen oder Blenden zur Entwässerung und Belüftung gleichmäßig auf Siebe aufgebracht, die ihn in die Pressen- und Trockenpartien der Papierwerks befördern.
Entscheidende Messstellen im Produktionsprozess
Bei den vielfältigen Produktionsabschnitten in der Zellstoffproduktion müssen zahlreiche pH- und Leitfähigkeitsmessstellen die Prozessqualität sicherstellen. So kann besonders während der Kochprozesse oder der Turmbleichung ein zu intensiver chemischer Aufschluss des Holzstoffs bzw. eine unzureichende Kontrolle von Bleichmitteldosierungen oder -rückständen die Fasern schädigen und ihre Festigkeit verringern. Solche Schäden können erst in abschließenden Qualitätskontrollen festgestellt werden, bei denen die Pappe oder das Papier auf Reißlänge, Durchreiß- und Berstfestigkeit geprüft wird. Daher muss die Intensität des chemischen Aufschlusses kontrolliert und geregelt werden. Dies geschieht mittels Leitfähigkeitsmessungen, mit denen die Weißlaugenkonzentration in den Zellstoffkochern überwacht wird.
Da das heiße Prozessmedium hochalkalisch und extrem verschmutzt ist, hat sich der Einsatz des induktiven Leitfähigkeitssensors SE655 aufgrund seines robusten Designs aus korrosionsbeständigem PEEK bewährt. Die Elektroden des Sensors, der für die Konzentrationsmessung von Säuren oder Laugen in stark verschmutzten und belagbildenden Medien konzipiert wurde, haben keinen direkten Kontakt zum Medium. Stattdessen verfügt SE655 über eine große toroidale Sensoröffnung, welche die Verschmutzungsgefahr auf ein Minimum reduziert. SE 655 ist für einen großen Messbereich von 0,002 bis 2000 mS/cm bei Temperaturen von -20 bis 110 °C ausgelegt und hält Drücken bis zu 20 bar stand.
pH-Messungen und Redox-Messungen in der Turmbleichung
Bei der Turmbleiche spielt die Redox- und pH-Messung eine übergeordnete Rolle. Der Bleichprozesse dient der Herauslösung verbliebener Rückstände wie restlichem Lignin. Dabei wird der Zellstoff in turmförmigen Behältern in mehreren Stufen abwechselnd mit Chlordioxid und Natriumhydroxid – oder bei moderneren, umweltfreundlicheren Verfahren mit Wasserstoffperoxid, Sauerstoff und Ozon – behandelt.
Bleichvorgänge basieren auf einem Elektronenaustausch zwischen den Bleichmitteln und den gebleichten Stoffen. Die Wirksamkeit der Bleichmittel hängt von der Größe ihres Oxidationspotentials ab, das sich durch Redox-Messungen ermitteln lässt. Weil die feststoffbelasteten Medien bei herkömmlichen Sensoren rasch zu Blockaden des Referenzsystems führen, wird hier der Memosens-Redox-Sensor SE564 verwendet, der dieses Risiko durch ein doppeltes Lochdiaphragma ausschließt. Sein Referenzsystem mit modernem Polymer-Elektrolyt gewährleistet die langzeitstabile Potentialmessung von –1500 mV bis 1500 mV.
Nach jedem Bleichvorgang wird der Zellstoff gewaschen und muss mittels pH-Messungen auf Bleichmittelrückstände untersucht werden, bevor er im nächsten Turm mit anderen Chemikalien in Kontakt kommt. Bei der pH-Kontrolle nach jeder Wäsche kommt der besonders wartungsarme Memosens-Sensor SE571 zur Anwendung, der für Messungen in Medien mit hoher Schmutzfracht und extremer Ionenstärke entwickelt wurde. Sein Bezugssystem steht mit dem Messmedium über ein PTFE-Ringdiaphragma mit minimiertem Verschmutzungs- bzw. Verblockungsrisiko in Kontakt. Zudem ist der Sensor durch einen eigenen Salzvorrat vor Auslaugung geschützt. Eine spezielle Ableitpatrone mit Silberionensperre verhindert die Vergiftung des Bezugssystems.
Rückgewinnung der eingesetzten Chemikalien
Für den wirtschaftlichen Betrieb von Zellstofffabriken ist die Rückgewinnung der eingesetzten Chemikalien entscheidend. Deshalb dient ein großer Anteil der Anlagen in der Zellstoffproduktion der Aufbereitung der Schwarzlauge, die bei der Filtration/Wäsche der gekochten und aufgeschlossenen Holzfasern anfällt. Die Schwarzlauge hat zunächst einen Feststoffgehalt bis zu 20 Prozent. Dieser wird mittels Eindampfanlagen auf ca. 80 Prozent erhöht, so dass die nun entstandene Dicklauge unter Zugabe von Natriumsulfat verbrannt werden kann.
Durch die Wandlung der dabei freigesetzten Energie in Strom und Prozesswärme decken die Zellstofffabriken einen großen Teil ihres Gesamtenergiebedarfes. Zugleich bleibt bei der Dicklaugenverbrennung eine aus Natriumcarbonat und Natriumsulfid bestehende Schmelze übrig, die durch Lösung in Wasser zur sogenannten Grünlauge wird. Bei der anschließenden Kaustifizierung (Ätzendmachung) der Grünlauge mit Kalkmilch entstehen Natriumhydroxid sowie Kalkschlamm, der durch Filtration oder Sedimentierung abgetrennt wird. Während die so aus der Grünlauge gewonnene Weißlauge wieder im Kochprozess verwendet wird, dient der abgeschiedene Kalk nach der Trocknung und einem Brand zur erneuten Weißlauge-Erzeugung.
Zur Messung der Leitfähigkeit, die neben verschiedenen Abschnitten der Zellstoffwäsche auch in unterschiedlichen Stationen im Schwarzlaugenkreislauf erforderlich ist, werden Memosens-Sensoren des Typs SE630 verwendet. Die Leitfähigkeitssensoren mit einem Messbereich von 10 µS/cm bis 20 mS/cm sind für einen hohen Druck bis zu 16 bar und Temperaturen bis 135 °C ausgelegt. Die können aufgrund ihrer großen chemischen, thermischen und mechanischen Beständigkeit sowie der einfachen Reinigungsmöglichkeit sehr flexibel eingesetzt werden. Im Kreislauf zur Chemikalienrückgewinnung dienen sie zum Beispiel auch der Durchbruchsüberwachung von Schwarzlauge-Boilern sowie zur Effizienzkontrolle bei der Grünlaugen-Kaustifizierung.
Sicherheit des technischen Personals
Viele Messstellen in der Zellstoffproduktion sind in Umgebungen positioniert, in denen der Aufenthalt technischen Personals auf ein zeitliches Minimum beschränkt werden muss. Durch die aggressiven Prozessmedien mit hohen Feststoffgehalten unterliegen auch die vorgestellten Sensoren trotz ihrer sehr robusten Auslegung eingeschränkten Standzeiten, reduzieren jedoch den Wartungsaufwand und damit die Verweildauer des Personals an den Messstellen erheblich: Durch die Verwendung vorkalibrierter Memosens-Sensoren entfällt die Kalibrierung vor Ort komplett. Zudem lassen sich Memosens-Sensoren – anders als festverkabelte Elektroden – aufgrund ihrer Schnellsteckanschlüsse mit Bajonettverschluss in kürzester Zeit an- und abstecken.
Da die Kontaktierung der Memosens-Sensorkupplungen, welche die Sensordaten und Speisespannung induktiv übertragen, vollkommen unempfindlich gegen Feuchtigkeit und Ablagerungen ist, entfällt zudem jegliches Kabelmanagement, das beim Austausch herkömmlicher Produkte erforderlich ist. Zur Inline-Messung mit Memosens-Sensoren stehen neben verschiedenen Prozessadaptionen für jeden Anwendungsfall auch die Wechselarmaturen der SensoGate-Baureihe zur Verfügung, die den Sensor intervall-getaktet und vollautomatisch herausfahren, reinigen, kalibrieren und erneut in den Prozess einfahren können.
Da die Spülkammer dieser Wechselarmaturen perfekt gegen den Prozess abdichtet, kann die Sensorwartung bei vollem Prozessdruck erfolgen. Eine besonders wirtschaftliche Lösung für den raschen Austausch von Inline-Sensoren bietet die manuell bedienbare Wechselarmatur SensoGate WA131M.
Return on Investment
- Die besonders robuste Auslegung und das verschmutzungsunempfindliche Design der pH- bzw. Leitfähigkeitssensoren wie SE571 bzw. SE655 gewährleisten zuverlässige, langzeitstabile Messungen auch bei pH-Werten über 12 bzw. in erheblich feststoffbelasteten Medien.
- In rauen Prozessumgebungen mit gesundheitsgefährdenden Chemikalien muss die Vor-Ort-Präsenz des technischen Personals auf das Notwendigste beschränkt werden.
- Anders als bei herkömmlicher Messtechnik erfolgt der Sensorwechsel bei Memosens in kürzester Zeit. Durch die Möglichkeit, Memosens-Sensoren im Labor vorzukalibrieren und durch den zeitsparenden kabellosen Steckanschluss vor Ort ist ein Sensortausch innerhalb weniger Minuten gewährleistet.
- Durch die Schnellanschlusstechnik und die automatische Übertragung aller im Sensorkopf gespeicherten Kalibrierdaten an das Messgerät entstehen beim raschen Austausch von Memosens-Sensoren keine relevanten Messlücken mehr, so dass Stillstandzeiten auf ein Minimum reduziert werden können.