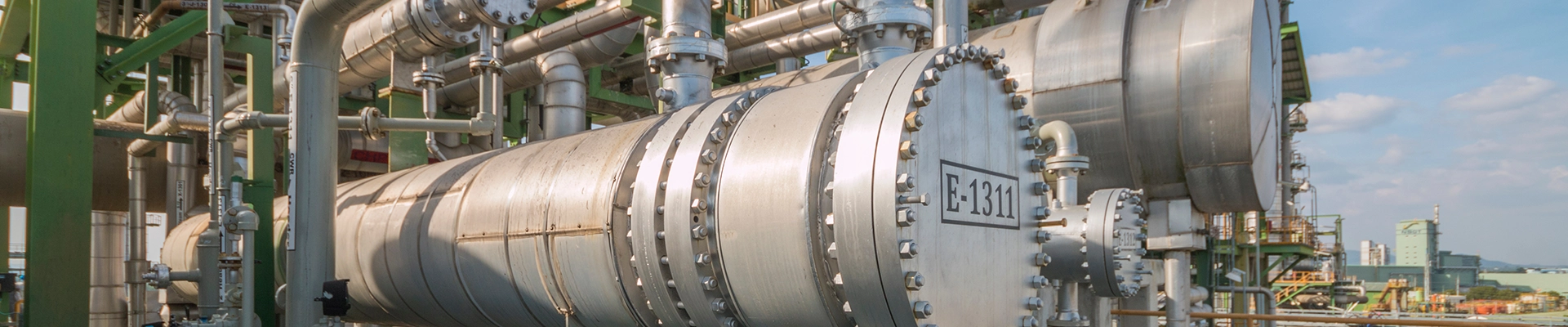
PROCESS ANALYTICS
Breakthrough Detection for Heat Exchangers
Breakthrough Detection for Heat Exchangers
Heat exchangers are used when liquid process media need to be cooled and/or dissipated heat needs to be recovered for other processes. Typical areas of application are steam generators and cooling towers in power plants (air as the cooling medium), as well as process areas in which plate heat exchangers and tubular heat exchangers are cooled with high efficiency by liquid cooling media.
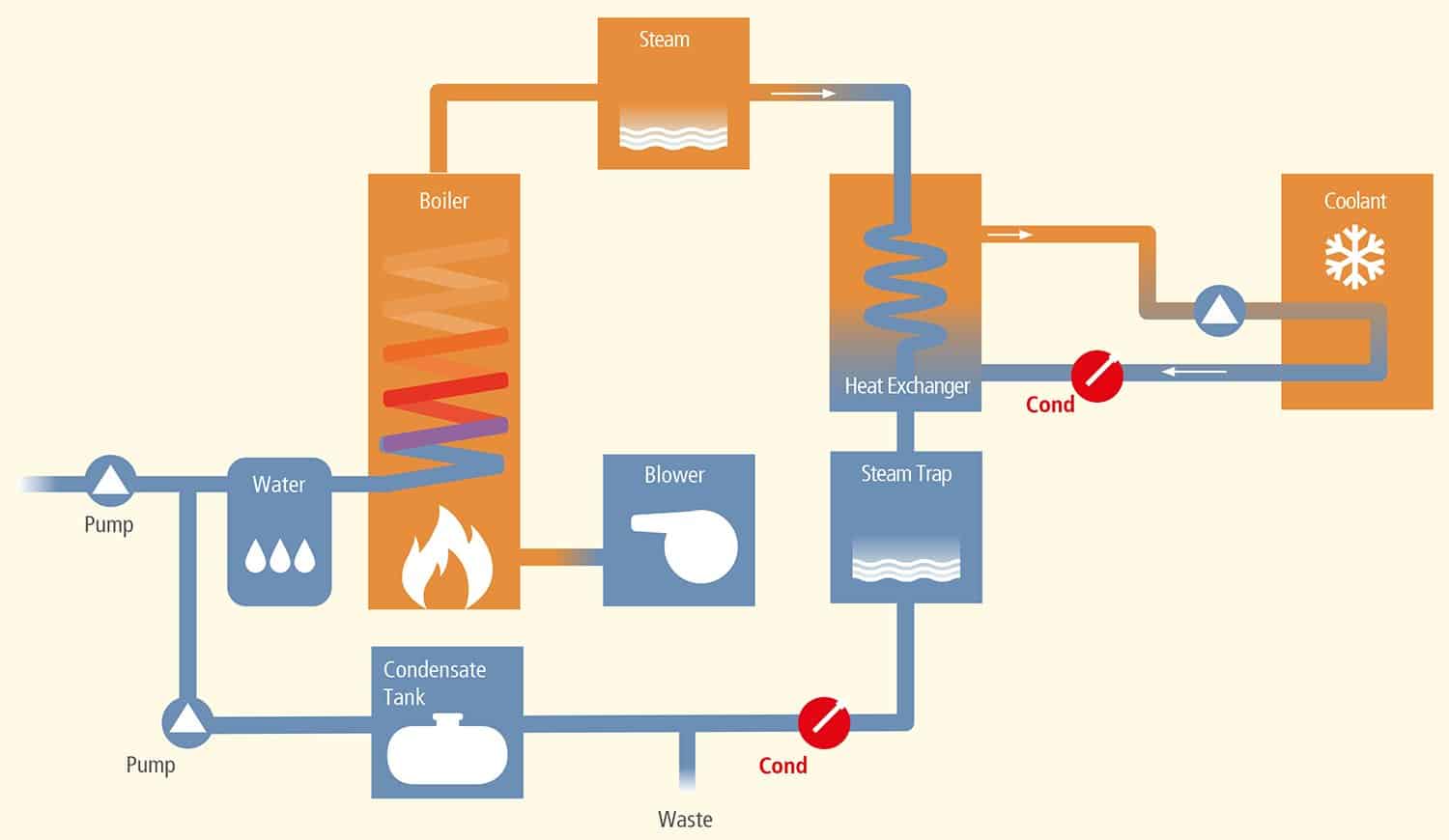
Conductivity Changes in the Cooling Water Indicate Breakthroughs in the Process
In heat exchangers, temperature exchange between material flows with different temperatures is realized using chamber or tube walls that are typically made of metal. They separate the flows but are permeable to heat. As a result of wear and corrosion, leaks in the partitions or tubes occur that may contaminate the cooling medium and cause significant damage to the plant. Contaminated cooling water could also enter the local water supply, leading to health hazards and severe penalties for system operators.
When steam is cooled down, it precipitates as condensation with a high degree of purity and in turn, very low conductivity. Since increased conductivity indicates contamination, conductivity measurement of condensate is a reliable method for checking that plants are functioning properly and detecting process breakthroughs.
As a rule, the measuring loops used here contain various conductivity sensors that are connected to multiple industrial transmitters in the enclosure. However, this setup requires extensive wiring and takes up lots of installation space in the enclosure.
Memosens digital sensor technology offers a space-saving, maintenance-free solution: With the Memosens SE615 conductivity sensor, contamination in the condensate can be established in the wide range of 10 µS/cm – 20 mS. The very narrow sensor with a PG 13.5 connection thread can be easily connected to the process inline in a matching fitting (e.g., ARI106) downstream to the heat exchanger where the temperature is no longer high.
For more stringent pressure and temperature requirements, Knick recommends using the SE604 (for the smallest measuring ranges from 0.001 – 1000 µS/cm) or SE630 (for larger measuring ranges up to 50 mS/cm) sensor with direct process connection via a G 1" or NPT thread.
All sensors have an integrated temperature detector for correct temperature compensation. When connecting the measuring loops to the control system, streamlined MemoRail transmitters (12 mm) significantly reduce the amount of space and cables needed in the enclosure for mounting on DIN rails. Moreover, two standard signal current outputs ensure the floating transfer of process-measured values and temperatures to the programmable logic controller.
Return on Investment
- Reliable monitoring of cooling water quality ensures plant efficiency and reduces the costs of repairs and water consumption.
- With precise conductivity measurement, leakage can be detected and remedied in time before it causes expensive damage to plants and the environment.
- Using MemoRail transmitters to transmit measured values and temperature values to the control system makes room in the enclosure and minimizes wiring complexity.