Reduced maintenance and increased accuracy through automated pH measurement with cleaning and calibration
In 2013, the Spanish company Azucarera was looking for an innovative solution for a particularly difficult measuring point in sugar production and found it in the fully automatic sensor cleaning and maintenance system cCare from Knick. The beet sugar production is an industrial process which starts by the beet washing that becomes raw juice. In its purification process there are two highly challenging points; the first and second carbonatation.
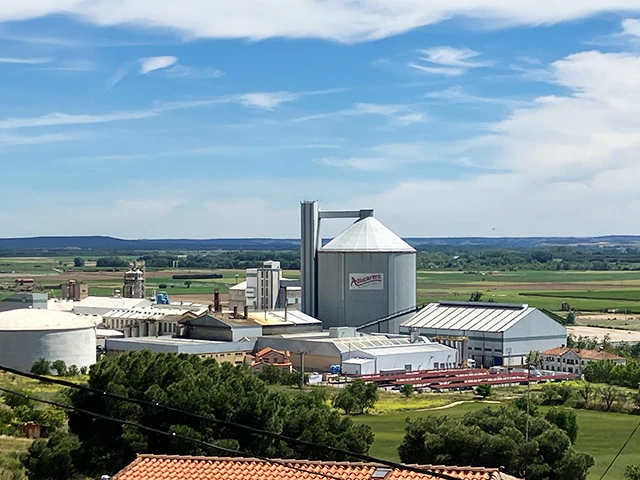
A successful cooperation for more than 10 years
The measuring system, which reliably provides accurate pH readings even under the adverse conditions of lime scale and high temperature, saves costs for lime, energy, manual maintenance and sensors.
After a very successful validation phase, Azucarera installed the first two systems in 2014, which have now been running for 10 years without any problems.
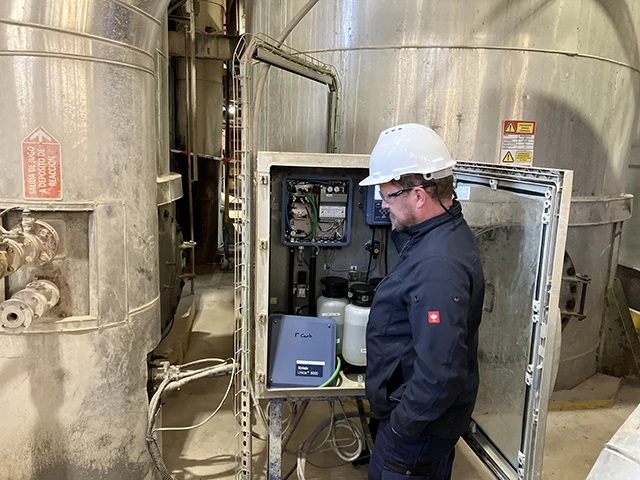
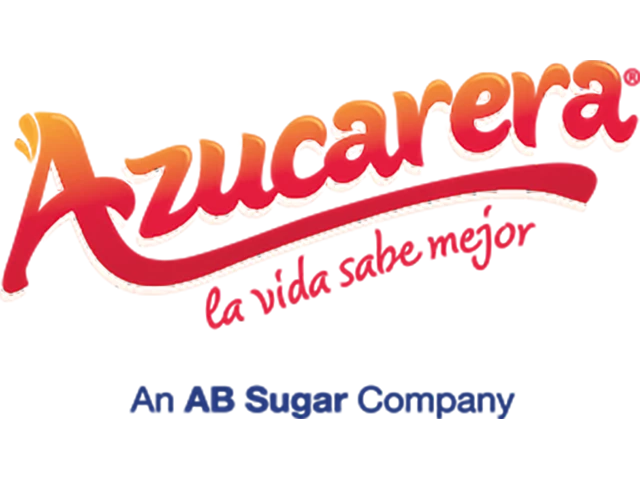
Customer
Azucarera is the leading sugar company in Iberia, with sugar beet sourced from a few thousand growers in Spain to the production sites in La Bañeza, Toro, Miranda de Ebro and Jerez de la Frontera.
Azucarera, part of the Sugar division of group of business AB Sugar.
Why Knick?
A proper temperature compensation factor is important to ensure the highest accuracy when measuring pH at high temperatures.
A proper (manual or automatic) cleaning and calibration of the pH sensor ensures a high accuracy and repeatability at the same time that increases its lifetime.
The challenge of pH measurement at 1st and 2nd carbonatations in sugar production
The purpose of 1st carbonatation is to introduce carbon dioxide and lime which causes lime to bind which removes impurities with precipitation. During this step, the pH value is kept between 10 and 11. To do so, carbon dioxide (from the lime kiln process) is introduced at approx. 70 °C so that the lime precipitates together with the impurities. However, the filter cake from this first carbonatation still contains considerable amounts of sugar and is therefore washed. The sugary wash water is returned to the first stage of the process together with the filtrate, but it still contains undesired calcium hydroxide.
2nd carbonatation is used to remove any remaining lime before moving to the evaporators in the thickening stage. The measurement of pH is critical to ensure the purification of the carbonatation juice. The remaining lime is precipitated at 90–95 °C in a second carbonatation process. If the pH value decreases too much due to the introduced carbon dioxide (carbonic acid in water), the lime decomposes to form hydrogen carbonate. If the value remains too alkaline, the precipitation is incomplete.
The efficiency of the carbonatation process strongly depends on the pH value at a temperature around 90 ºC, with the formation of deposits due to lime, non-sugar particles and sticky syrup. The life of the electrodes is shortened by abrasion and blocking of the reference system.
Therefore, the measuring points must be checked several times a day and the pH sensors must be cleaned frequently with an acidic cleaning agent, such as amidosulfonic acid.
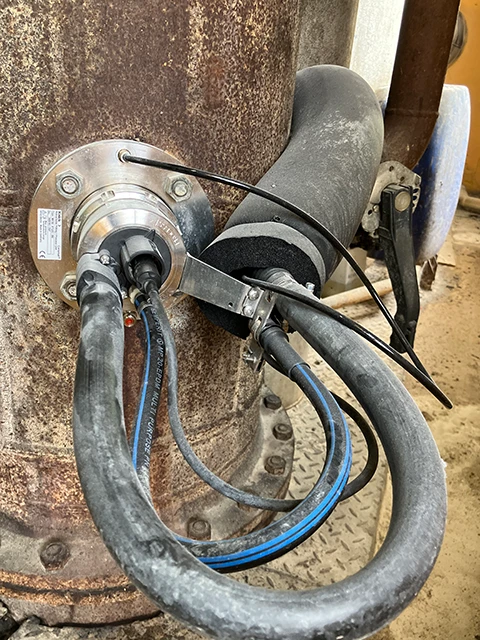
The Ceramat retractable fittings in the 1st carbonatation ...
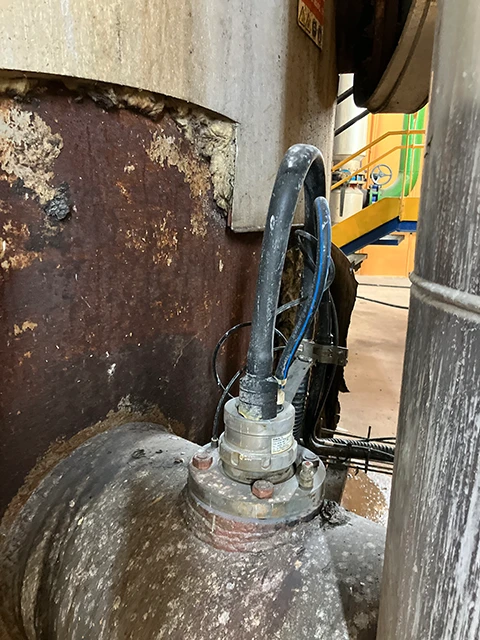
...and 2nd carbonatation have been in use since 2013.
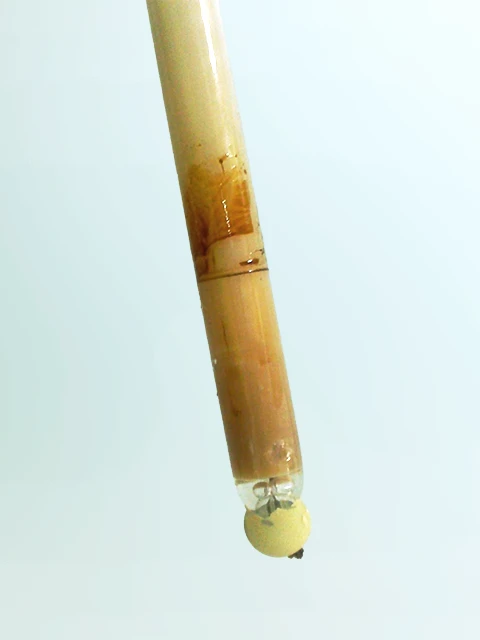
The pH sensors must be cleaned frequently with an acidic cleaning agent.
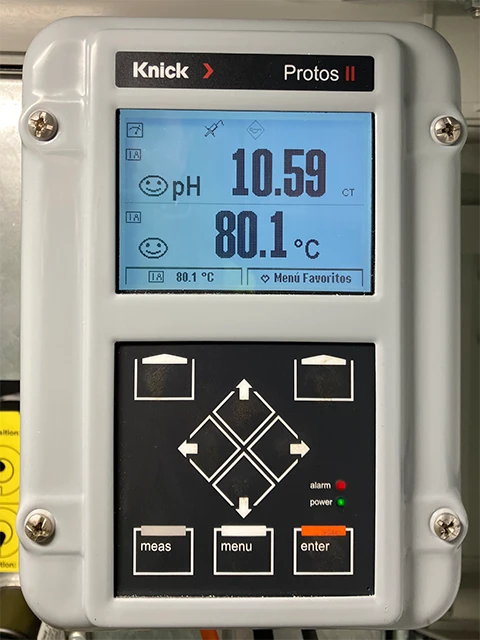
pH measurement around 90 ºC
Solution and customer benefit – Substantial saving costs for maintenance, sensors, lime, and energy
Until the installation of the automatic measuring point, the customer took a sample every hour for 3–4 months during the sugar campaign and brought it to the laboratory for checking. This was very time consuming and also inaccurate, because the effects of the temperature compensation could not be considered properly and the response time was too long.
cCare – Fully Automated Sensor Maintenance System
With the cCare system, the pH sensor is cleaned every 8 hours in the 1st carbonatation, every 2 hours in the 2nd carbonation, and calibrated 3 times per week. Everything is fully automatic, and no manual intervention is required. Personnel resources (maintenance costs) are minimized and the Memosens pH sensor is now working for at least one beet sugar campaign of 3–4 months. Reliability and robustness of the system is really proofed.
The increased accuracy leads to great savings in production. This is possible thanks to the cleaning and calibration on site and the use of the temperature compensation table for this particular medium.
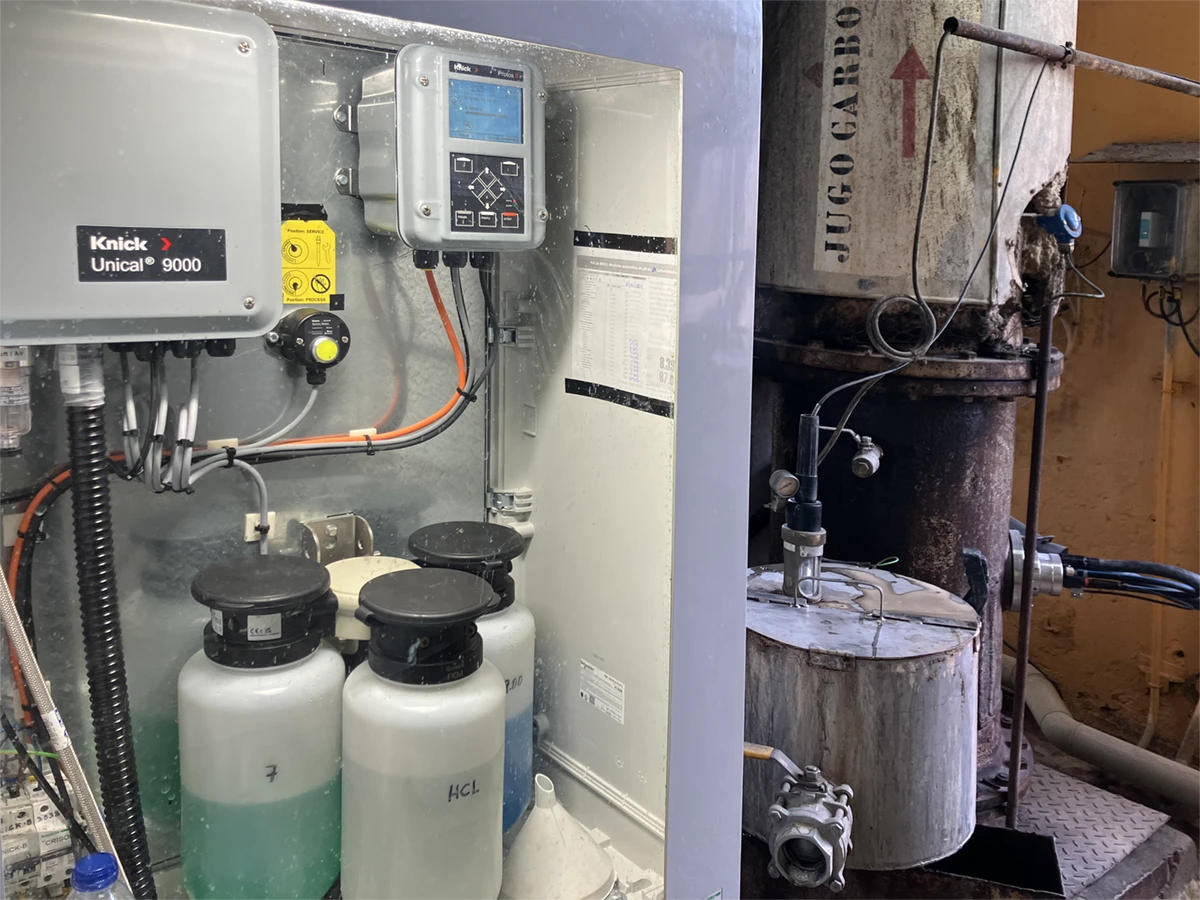
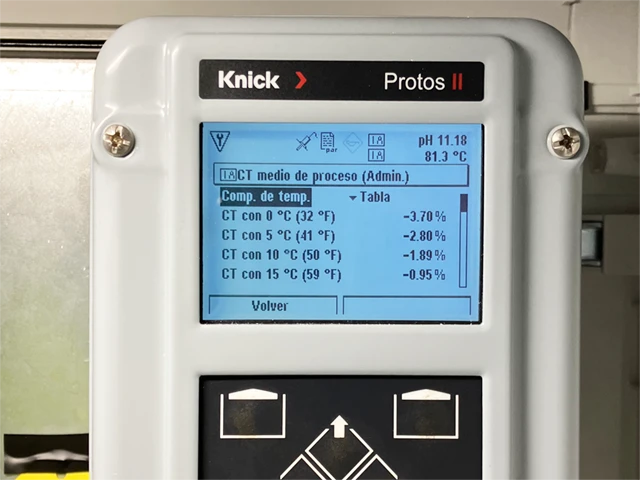
Good to know: Temperature Compensation
The pH value is temperature dependent, and transmitters use to perform the temperature compensation based on a generic table. In this case Protos allows the introduction of a specific table for this process and consequently the pH value is calculated with the highest accuracy.
It is possible to obtain pH values from the inline measuring system, which can be compared directly with the pH values of the reference samples in the laboratory. If this temperature compensation was not used, pH values of different temperatures would be compared, which would lead to misinterpretations and errors.
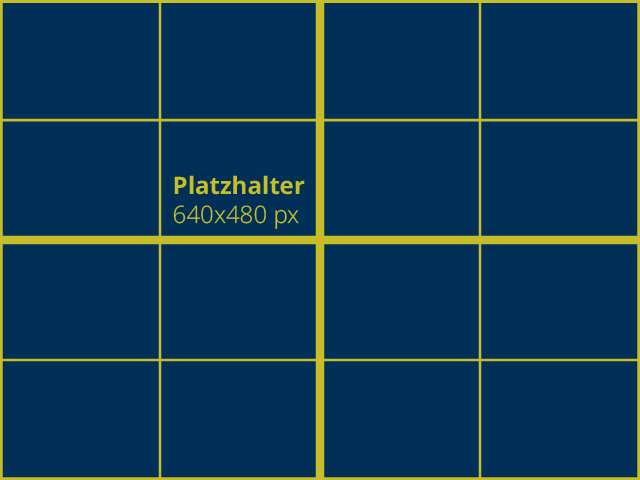
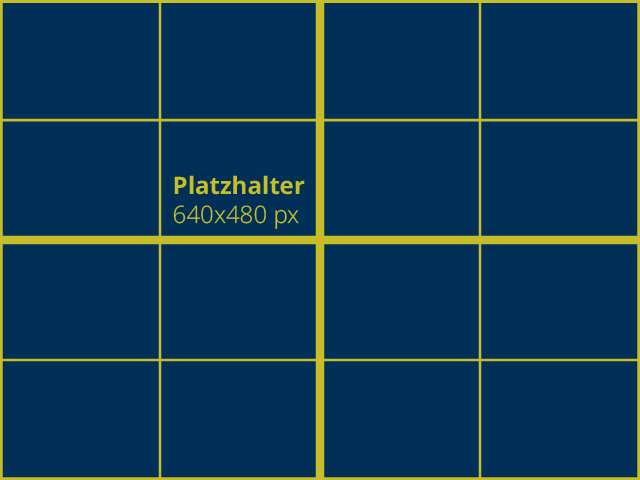
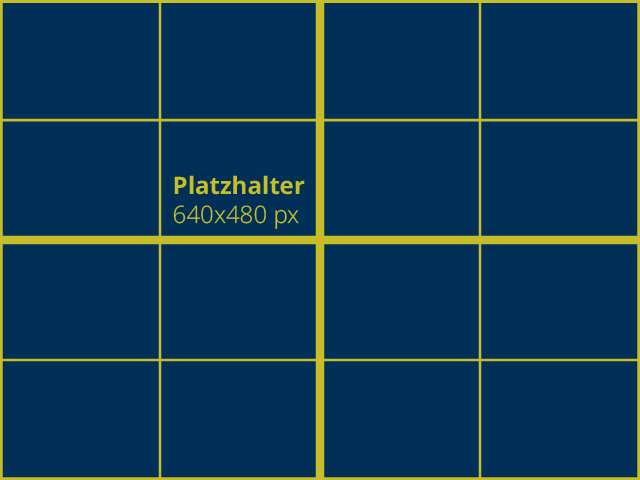
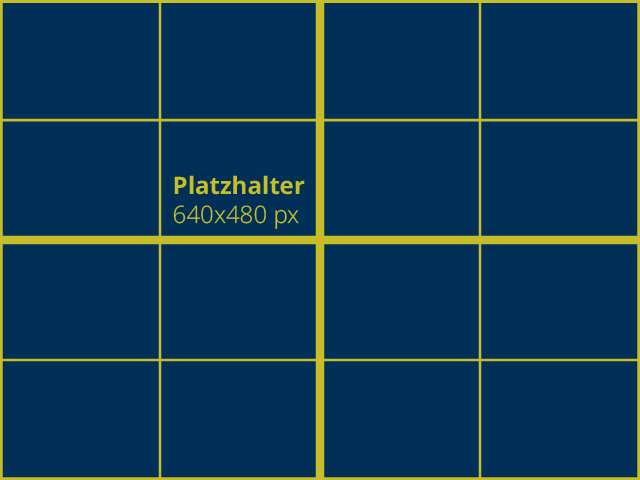
Products
More information needed? We look forward to hearing from you!
Contact Us