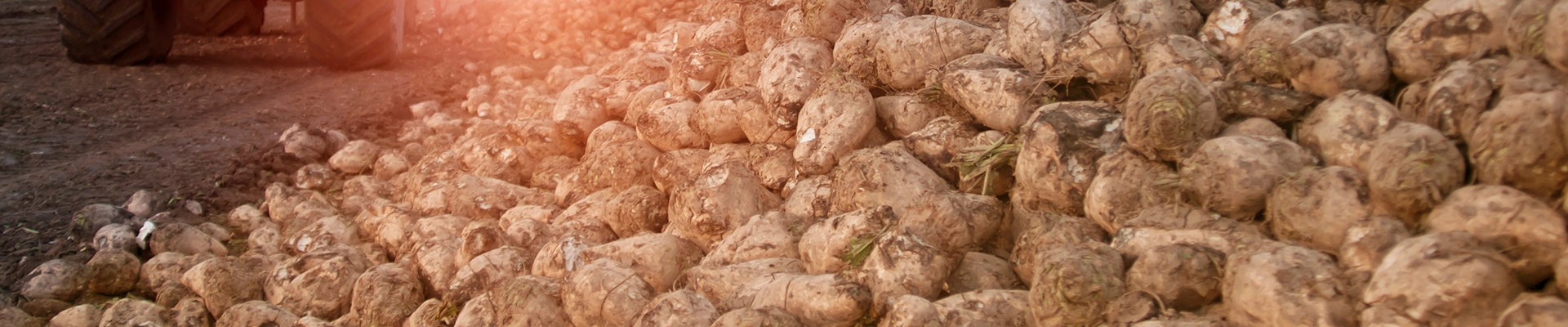
PROCESS ANALYTICS
Monitoring Sugar Production
Monitoring Sugar Production
The sugar industry campaign begins right after the sugar beet harvest and lasts around four months. First, the beets are washed in a solution containing lime and chopped into slices. Next, they go through the tower extractor, where hot water is added to extract the sucrose. The extracted raw juice is still highly contaminated with organic and inorganic substances that are precipitated and filtered out during the juice washing and carbonatation processes, in which the lime slurry and carbon dioxide are introduced to precipitate and filter out the impurities. The washed “thin juice” is thickened in evaporators in several stages to yield syrup with a substantially higher sugar content. The thick juice goes through a crystallizer and a centrifuge, where the syrup is transformed into white, crystalline sugar.
The pH measuring loops are subjected to considerable strain due to thick lime deposits, high temperatures, and frequent rinsing with acidic cleaning media. However, they must ensure maximum availability since the processes cannot be interrupted during an ongoing campaign.
In sugar production, the high-cost drivers are fossil fuels and burning the lime on site. With highly available and precise pH measurement, lime consumption, and in turn, both the energy requirements and degree of plant contamination are significantly reduced.
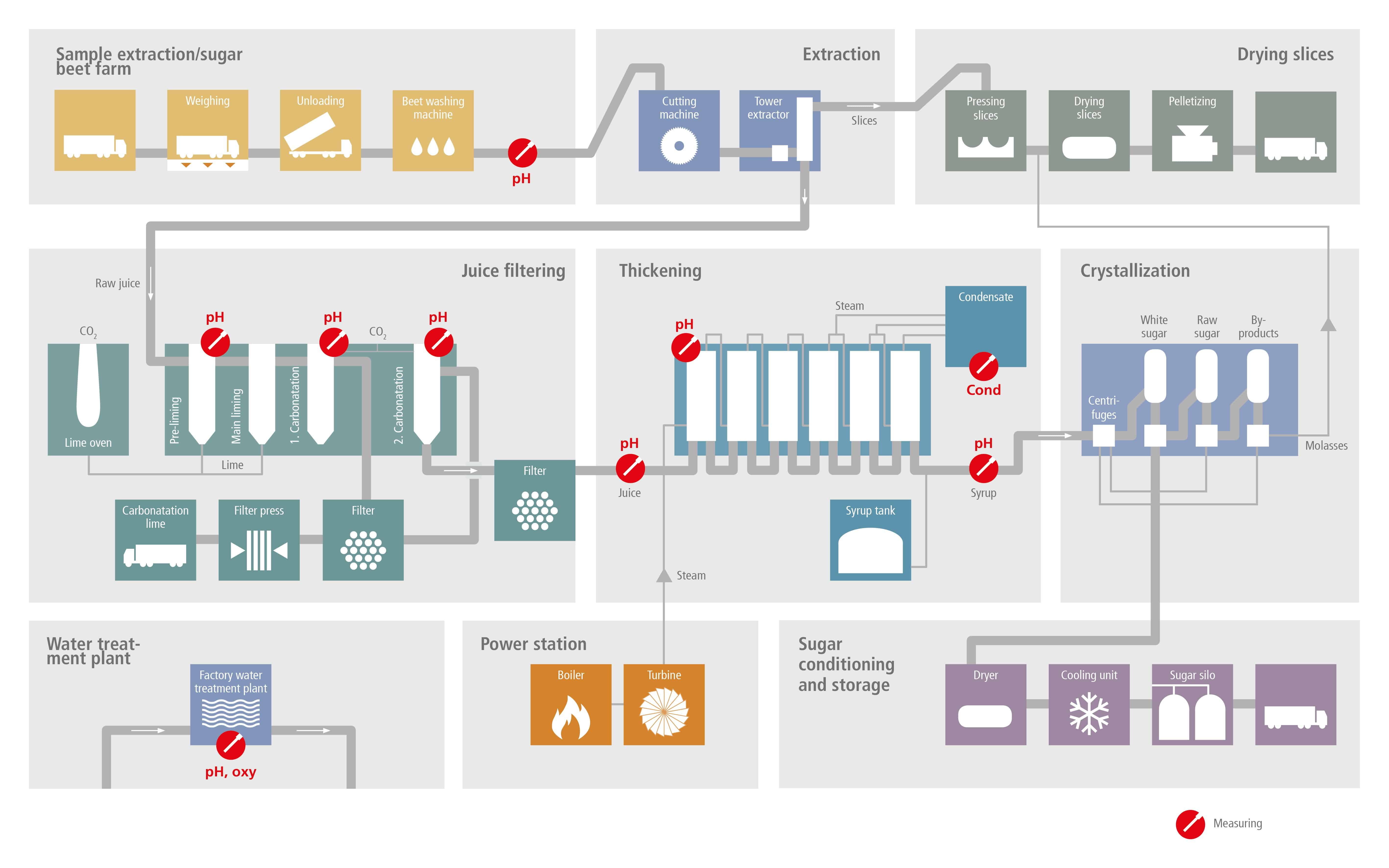
Substantial Savings on Lime and Energy with the Increased Availability of Memosens Measuring Loops
Sugar production places extreme requirements on pH sensors. During the beet washing phase, in which water is made alkaline by adding lime to neutralize the acidic soil from the field that is still clinging to the beets, lime is metered based on pH measurement.
In view of the moist and contaminated environment and the need to frequently clean the sensors with acid, the SE555 pH sensor with the inductive measurement transmission typical of Memosens avoids all problems with contaminated, moist, or encrusted contacts. And with the option to pre-calibrate the Memosens sensors in the laboratory, on-site calibration under adverse ambient conditions is no longer necessary.
Further, the extensive Memosens diagnostic functions record all the standard and operating data saved in the sensor head. Control of sensor operating time, sensor wear, remaining lifetime, maximum temperature, the adaptive calibration timer, and the calibration and adjustment data significantly increase availability. Pre-calibrated Memosens sensors have a service life of up to 40% longer than conventional products.
Depending on the distance between the beet washing station and the main facility, an automated measuring solution with the extremely resistant and maintenance friendly Ceramat or SensoGate retractable fittings from Knick, which accommodate all Memosens sensors, can reduce the personnel costs of measuring loop maintenance. The digitization of the measured value inside the sensor head makes the process much easier and enables seamless measured value transmission – even for cable lengths of up to 100 m.
During carbonatation, the measuring loops are particularly contaminated by the sticky juice extracted from the sugar beets and its initially high solid content.
Alongside this organic contamination, extreme lime deposit formation and temperatures of up to 95 °C adversely affect the measuring loop during juice cleaning in particular.
By the end of the sugar campaign, the lime deposits can be several decimeters thick. For this reason, the sensors must often be rinsed with acidic solutions and this shortens their service life. This is the point at which the SE555 proves itself: It has a ceramic junction in combination with a pressurized reference as protection against aggressive rinsing media.
Since the pH sensors must be checked and cleaned several times a day during the campaign, automating the measuring loops with the Ceramat WA150 remote calibration probe has proven to be an excellent solution for extreme applications. In conjunction with the Unical 9000 automatic controller, the sensor is fully automatically cleaned with acid and calibrated at regular intervals.
The Ceramat process fitting consists of virtually indestructible aluminum oxide ceramic that opens and closes by rotating and a corrosion-resistant, carbon-reinforced stationary molded enclosure made of PEEK or PVDF. Even in abrasive media, the flat sealed surface of the hard ceramic does not show wear.
High mechanical strength and temperature resistance, as well as nearly universal chemical resistance, ensure smooth operation even under difficult conditions with an extremely high volume of contaminants. The retractable fitting is equipped with a pneumatically moved elastomer bellows to counter the thick incrustation of the wetted Ceramat components. At regular intervals, the bellows blasts away the solidified deposits at the sensor opening.
Return on Investment
- High-availability Memosens measuring loops ensure the continuity and quality of your processes and significantly reduce resource consumption with precise, continuous measurements.
- The pre-calibration function also helps you save costs, since with Memosens, sensor service life is up to 40% longer in comparison to conventional products.
- Using Memosens sensors in conjunction with the Protos process analysis system and the Unical automated measuring, cleaning, and calibration system from Knick, you can even automate measuring loops in which conventional automation solutions typically fail due to adverse ambient conditions and heavy contamination.
Associated Products
Associated Industries and Applications
Knick offers a solution to extending the service life of wear-prone pH sensors, particularly in cases of difficult media: cCare. The cCare system ensures accurate measured values and reduced maintenance and material costs thanks to the fully automated cleaning and calibration of pH sensors.
Latest Blog Post
SE555X/1-NMSN
SE555X/4-NVPN
SE555X/2-NMSN
SE555X/2-NVPN
SE555X/4-NMSN
SE555X/2-AMSN
SE555X/1-AMSN
SE555X/1-NVPN
SE555X/1-NS8N
SE555X/3-NVPN
SE555X/2-NS8N
SE555X/3-NMSN