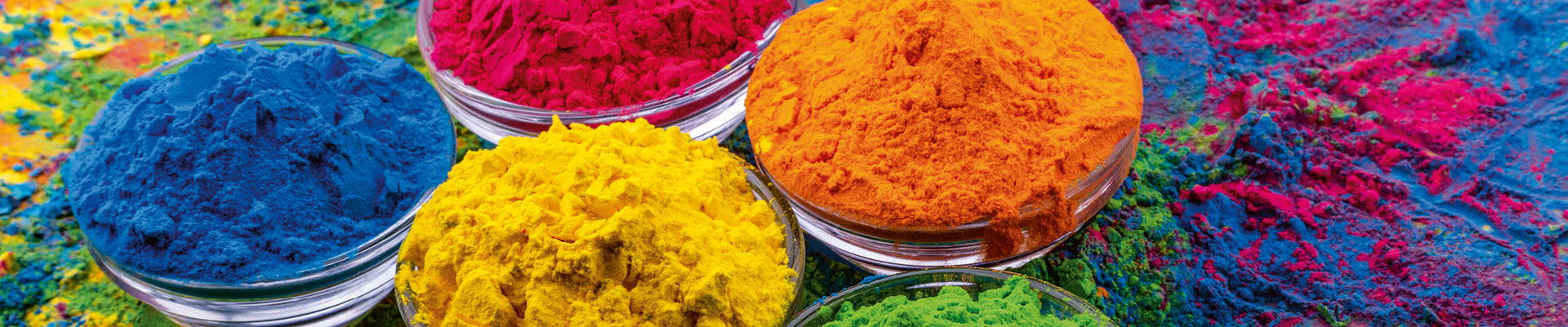
PROCESS ANALYTICS
pH Measurements in the Dye Synthesis of Azo Dyes
pH measurement during dye synthesis of azo dyes with Knick’s Ceramat fitting
Azo dyes make up the largest group of synthetic dyes by number. They are used as food dyes, artists’ colors, basic colors for four-color printing (yellow and magenta), as well as textile dyes on a large scale. More than 350,000 tons of azo dyes are used worldwide for the dyeing of natural fibers.
Keyfacts Application
Sector
Azo dye production 24/7
Application
cCare - fully automated sensor maintenance for dye syntheses in which virtually all essential reaction steps are pH-dependent, so that optimization of the of the product yield based on a reliable and low-maintenance pH measurement.
Measured Parameter
pH
Key Requirements
The extreme conditions for the measuring point are as follows:
- pH = 1, hydrochloric
- Temperature = 90°C,
- Pressure = 6 bars.
- The pH electrodes have a service life of 8 h up to several weeks.
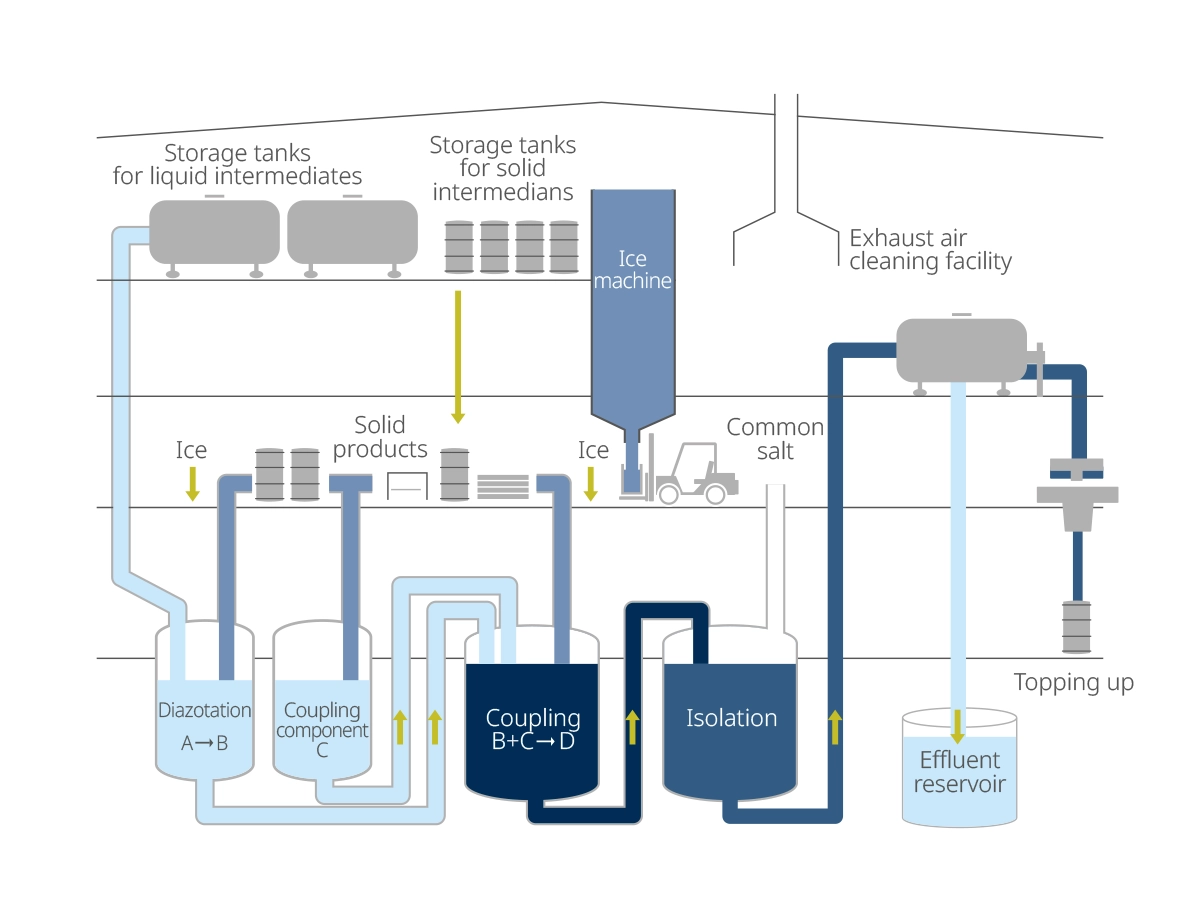
Measurement requirements
Dye syntheses in modern plants run around the clock in four shifts. Virtually all essential reaction steps are pH-dependent so that the optimization of product yield is based on a reliable, low-maintenance pH measurement. The diazotation reaction requires much hydrochloric acid and is therefore correspondingly corrosive. The reactors are protected by an enamel coating, the coupling reactors also by a rubber coating.
The extreme conditions for the measuring point are as follows:
- pH = 1
- Temperature = 90 °C
- Pressure = 6 bar.
The pH electrodes have a service life of eight hours up to several weeks. Automation of these measuring points with conventional retractable fittings is only possible when Hastelloy C4 is used. Nevertheless, these expensive fittings require high maintenance effort. The fitting must be removed and serviced several times a year.
Solution
The Ceramat WA150 retractable fitting together with the Unical 9000 automatic cleaning and calibration system allows complete automation of this difficult measuring point with maximum availability. The Ceramat fitting consists of a corrosion-proof, ultrahard, superpolished, rotating ceramic part and a corrosion-resistant, carbon-reinforced, non-moved plastic housing made of PEEK.
Why Knick?
After 24 months run time the Ceramat does not show any wear on seals, probe housing, or other parts.
Matching Products
Related Industries and Applications
Overview of specific applications and product solutions in different areas of industrial chemicals.