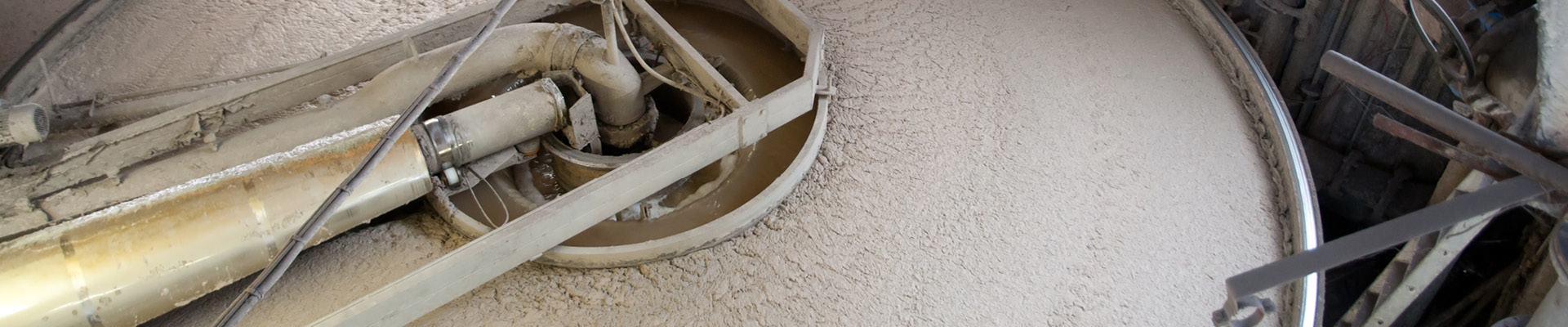
PROCESS ANALYTICS
Pulp and Paper Production
Process Control in Pulp and Paper Production
In pulp production, significant amounts of caustic soda solution and chlorine dioxide are used in addition to numerous chemicals.
The pH sensors used for process control are subject to high stress since they are in continuous contact with caustic chemicals.
In addition, the service life of the sensors is limited due to the high fiber and suspended matter content of the process media. After a short time, thick deposits and incrustations form on the measuring electrodes.
The harsh process environment characterized by aggressive chemicals and a high level of contamination requires measuring loops that enable fast, simple sensor replacement in a minimum amount of time.
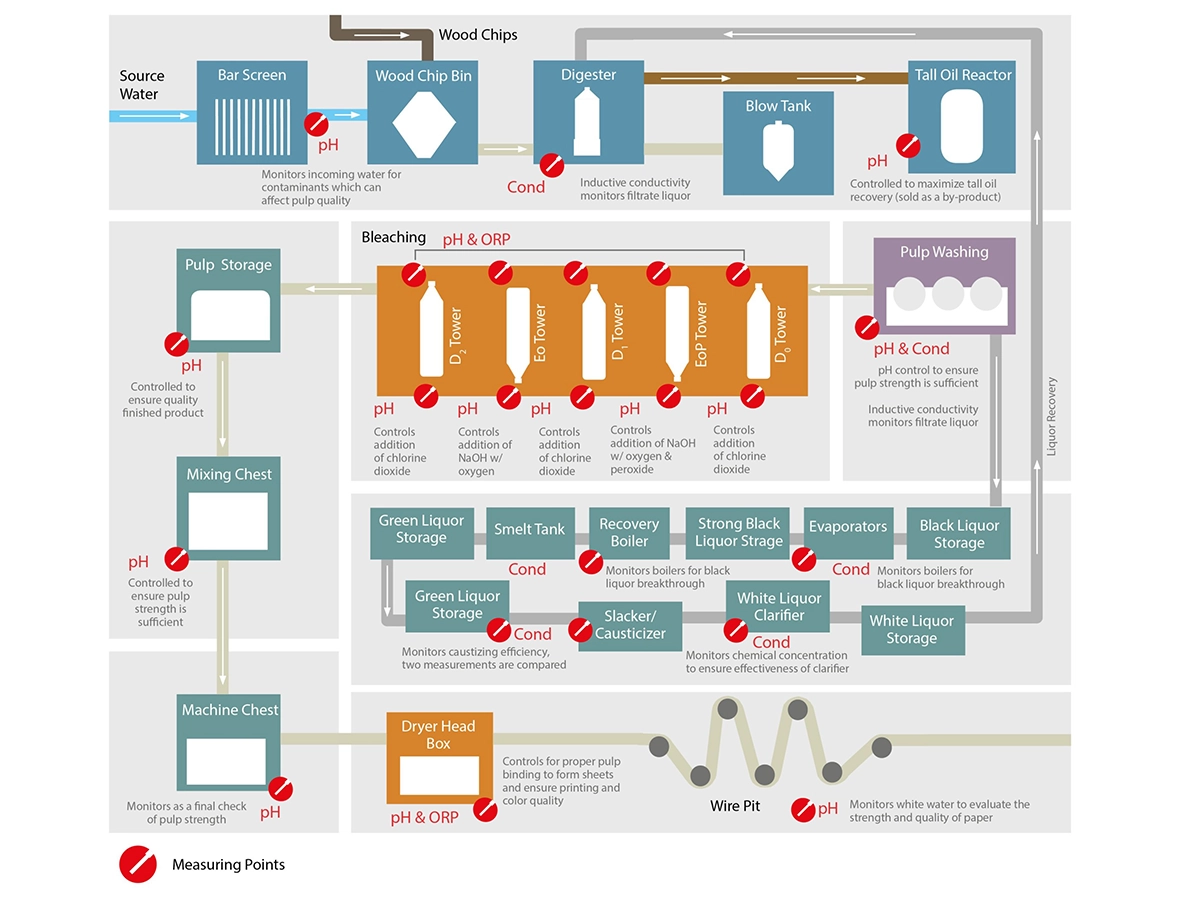
Measuring Sensors for Process Control in Pulp and Paper Production
All About Pulp Production
Since pulp paper and the sulfate and sulfite process were invented in the mid-19th century, it has been possible to produce paper based on wood. In the kraft and sulfite process, mechanically shredded wood is chemically macerated by boiling it in caustic soda solution and solutions of sodium sulfide and sulfur dioxide in order to release the cellulose fibers it contains from other, undesirable components. These components include wood-forming lignins, polysaccharides called “hemicellulose,” resins, and minerals. The cellulose fibers in the form of an aqueous solution are cleaned and bleached in different multi-step sequences, and the separated resins are used to manufacture tall oil, which is used in the production of soap and lacquers after it is refined.
Sequences in Pulp and Paper Production
Alongside the basic raw material properties, the quality of the multi-faceted cleaning and mixing process that pulp passes through during processing plays a significant role in product quality. It primarily includes cooking pulp in the “white liquor” used in the kraft process, subsequent filtering and washing the cooked pulp on filter lines, and a multi-stage bleaching process in which the pulp is treated with alternating oxidants.
Next, the pulp is refined in the stock preparation process. First, it is combined with different fibrous materials (depending on the recipe) in the mixing vat and ground. Fillers like kaolin, calcium carbonate, glue, and dyes are added in order to achieve the desired properties of the finished paper. In the headbox, nozzles or apertures evenly deposit the stock on screens for dewatering and drying, which transport it to the pressing and drying sections of the paper factory.
Key Measuring Loops in the Production Process
In the various production segments in pulp production, many pH and conductivity measuring loops must ensure the quality of the process. For example, the pulp may be subject to intense chemical pulping during the cooking or bleaching process or inadequate control of bleaching agent metering or residue could damage the fibers and reduce their strength. These kinds of damage cannot be determined until the final quality control stage, in which the cardboard or paper is tested for breaking length, tear resistance, and bursting strength. This is why the intensity of chemical pulping must be checked and regulated through conductivity measurements, which monitor the white liquor concentration in the pulp cookers.
The hot process medium is highly alkaline and highly contaminated, and due to its robust design and corrosion-proof PEEK material, the SE655 inductive conductivity sensor has proven itself in use. The electrodes of the sensor were designed for measuring the concentration of acids or alkalies in highly contaminated and deposit-forming media and do not have direct contact with the medium. Instead, SE655 has a large, ring-shaped sensor opening that reduces the risk of contamination to a minimum. SE655 is designed for a wide measuring range of 0.002 to 2000 mS/cm at temperatures of -20 to 110 °C and can withstand pressures of up to 20 bar.
pH Measurements and ORP Measurements in the Bleaching Phase
During the bleaching phase, ORP and pH measurements are a priority. In this phase, residual substances like the remaining lignin are released. The pulp is treated with alternating chlorine dioxide and sodium hydroxide in tower-shaped vats – or in more modern, environmentally friendly methods, with hydrogen peroxide, oxygen, and ozone.
Bleaching treatments are based on an electron exchange between the bleaching agents and the bleached stock. The effectiveness of the bleaching agent depends on the level of its oxidation potential, which can be determined by ORP measurements. The media are loaded with solid substances, and the reference system of conventional sensors can quickly become clogged. Therefore, the Memosens SE564 ORP sensor, which excludes this risk thanks to a dual open junction, is used here. Its reference system with modern polymer electrolyte ensures potential measurement of -1500 mV to +1500 mV with long-term stability.
After every bleaching operation, the pulp is washed and must be examined for residual bleaching agent with pH measurements before it comes into contact with the other chemicals in the next vat. In the pH check after each washing operation, the particularly low-maintenance Memosens SE571 sensor is used. It was developed for measuring in media with a high dirt load and extreme ionic strength. Via a PTFE ring junction with a minimized soiling or clogging risk, its reference system is in contact with the process medium. Further, the sensor has its own salt reservoir to protect it against leaching. A special dissipation cartridge with a silver ion trap prevents the reference system from being poisoned.
Recovery of the Chemicals Used
For the economical operation of pulp factories, it is crucial to recover the chemicals used. This is why a large proportion of the plants in pulp production are used for treating the black liquor resulting from the filtration/washing of the cooked and extracted wood fibers. Black liquor initially contains up to 20 percent solids. Using evaporators, this is increased to approx. 80 percent so that, with the addition of sodium sulfate, the newly created thick liquor can be burned.
Pulp factories cover a large part of their overall energy consumption by converting the released energy into electricity and process heat. At the same time, a smelt primarily consisting of sodium carbonate and sodium sulfide remains after thick liquor is burned. When dissolved in water, it becomes “green liquor.” In the subsequent causticizing stage, the green liquor is reacted with lime slurry to create sodium hydroxide and lime mud, which is separated by filtration or sedimentation. The white liquor extracted from the green liquor is reused in the cooking process while after drying and burning, the separated lime is used again to produce white liquor.
Memosens SE630 sensors are used to measure conductivity, which is necessary in different stations in the black liquor cycle in addition to the various segments of pulp washing. The conductivity sensors with a measuring range of 10 µS/cm to 20 mS/cm are designed for high pressures up to 16 bar and temperatures up to 135 °C. They can be used flexibly thanks to their high chemical, thermal and mechanical resistance, and the simple cleaning option. In the chemical recovery cycle, for example, they are used for breakthrough monitoring in black liquor boilers and efficiency control in green liquor causticizing.
Safety of Technical Personnel
Many measuring loops in pulp production are located in environments in which technical personnel must spend as little time as possible. Thanks to the aggressive process media with a high solids content, the sensors presented here are subject to a limited service life despite their robust design. However, they reduce maintenance time and in turn, the length of time personnel must remain at the measuring loops. By using pre-calibrated Memosens sensors, on-site calibration is no longer necessary. Further, unlike permanently wired electrodes, Memosens sensors have quick push-in connections with a bayonet coupling and can be pushed in and pulled out in the shortest time possible.
The contacting of Memosens sensor couplings that inductively transmit sensor data and supply voltage is fully resistant to moisture and deposits, making the cable management that is required when replacing conventional products completely unnecessary. In addition to the different process connections for every application, there are retractable fittings in the SensoGate series for inline measurement with Memosens sensors. They extend, clean, and calibrate the sensors and retract them back into the process – at timed intervals and fully automatically.
Because the rinsing chamber of these retractable fittings provides a perfect seal against the process, sensor maintenance can be carried out at full process pressure. The manually operable SensoGate WA131M retractable fitting is a particularly economical solution for the fast replacement of inline sensors.
Return on Investment
- The particularly robust design and soiling resistance of pH and conductivity sensors like SE571 and SE655 ensure reliable measurements with long-term stability, even with pH values over 12 or in media that are significantly loaded with solid substances.
- In harsh process environments with chemicals that are hazardous to health, the on-site presence of the technical personnel must be limited to what is absolutely necessary.
- Unlike conventional measuring technology, Memosens sensors are replaced in the shortest time possible. With the option to pre-calibrate Memosens sensors in the laboratory and thanks to the time-saving cable-free push-in connection on site, sensors can be replaced in only a few minutes.
- Thanks to quick connection technology and the automatic transmission of all calibration data stored in the sensor head to the transmitter, the fast replacement of Memosens sensors eliminates all relevant measurement gaps and reduces downtime to a minimum.