cCare pHarma
While production in the chemical industry is mainly continuous, in BioPharma processes this is mainly done in batches. The measuring media are usually not aggressive, but the requirements for sterility and cleanability of the equipment as well as for the control of the process parameters, especially in the upstream process, are very high. There are numerous possible errors which, in the worst case, can lead to a complete batch loss.
For BioPharma applications, the cCare modular system provides tubing, connections and modules in FDA-approved material that are optimized for the strict hygiene requirements.
Automation standardizes the cleaning and calibration of sensors, automatically documents all process steps (audit trail) and thus eliminates operating and data transmission errors. As a result, cCare for pharma significantly reduces the risk of batch losses due to human error.
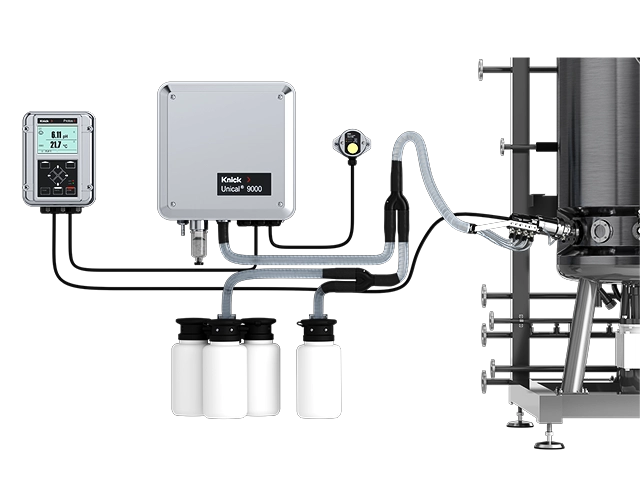
Is manual pH calibration a game of chance?
Yes, unfortunately it can be.
On the occasion of the cCare for Pharma Systems trade show presentation at ACHEMA 2024, we once dared to create a slightly provocative film: A slot machine plays with the risks and potential for errors caused by manual pH sensor calibration for the batch.
What does a batch loss cost your company?
Why Knick?
cCare for Pharma
- automates and standardizes cleaning, and calibration for reliable pH measurements at any time
- maximizes yield by minimizing sensor drift
- provides seamless documentation for optimal compliance due to Audit Trail
- reduces the risk of losing batches due to human influences
With automatic pH measurement to optimize efficiency and costs
In many industrial processes, the pH value is one of the most important control parameters. But at the same time, pH measuring points require intensive maintenance. In many processes and media, sensors must be cleaned and calibrated several times a day. This minimizes sensor drift and delivers measured values that can be trusted.The time required to do this, in an era characterized by staff shortages, possible transmission errors in the case of manual work steps, and the subsequent mistake of rejecting batches, makes it essential to start thinking about optimization activities supported by automation.
However, many companies still calibrate pH sensors manually. The process is very time-consuming, requiring an employee to "invade" the cleanroom, remove the sensor, clean it, place it in a series of different buffer solutions, and wait until the pH value is stable. This poses the risk of mechanical damage to the sensor, and the employee's actions may also influence the process. For example, whether the sensor is swirled or simply immersed in the buffer solution makes a big difference. Finally, the sensor must be reinstalled, and the system must be cleaned or sanitized.
Automatic, standardized pH sensor calibration
Knick offers a solution for automatic pH sensor maintenance that eliminates the disadvantages of manual calibration. The system of automatic pH measuring loops, which Knick markets under the name "cCare", performs a standardized calibration fully automatically and sends all values and the calibration report to the process control system. As a result, all batch data is digitally documented by an audit trail without the risk of manual transmission errors.All sensor maintenance is performed without manual intervention and can be triggered by the process control system or on-site at the transmitter. The sensor is automatically moved into the retractable fitting's calibration chamber, cleaned, and sanitized, and then returned to the process.
As a result, the automatic system always performs sensor adjustments in exactly the same sequence. cCare does more than just extend sensor service life and reduce labor costs. Its fully automated sequences also ensure more accurate pH measurements, which directly impact the safety and yield of the biopharmaceutical process. The cCare system is also the only sensor maintenance system on the market that is fully approved for use in Zone 1 hazardous locations.
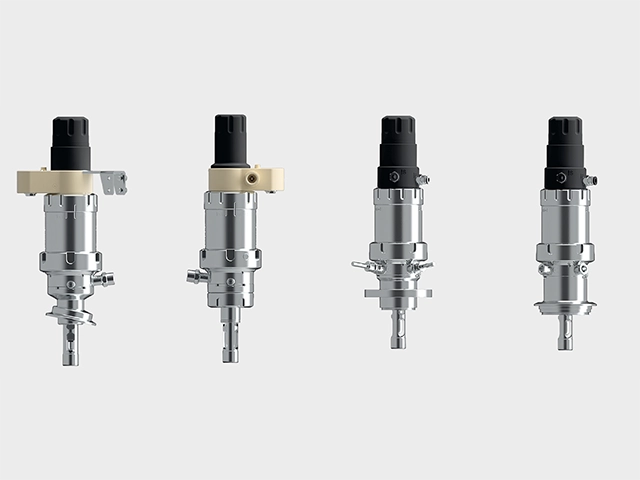
Pharma solutions - customized retractable fittings
Our well-thought-out fitting systems allow ideal solutions with regard to process connection, immersion depths and materials. Thus, our retractable fittings meet all requirements due to process media, hygienic demands and installation situations. In addition, we can also customize fittings for our customers.
SensoGate - the best retractable fitting for hygienic requirements
Thanks to its patented interlock system, SensoGate ensures process safety at all times, so that sensor replacement can be carried out without interrupting the process. A sophisticated cyclone rinsing thoroughly cleans the sensor, the seals, and the calibration chamber. SensoGate has no dead spaces that are not cleaned by rinsing, SIP and CIP.
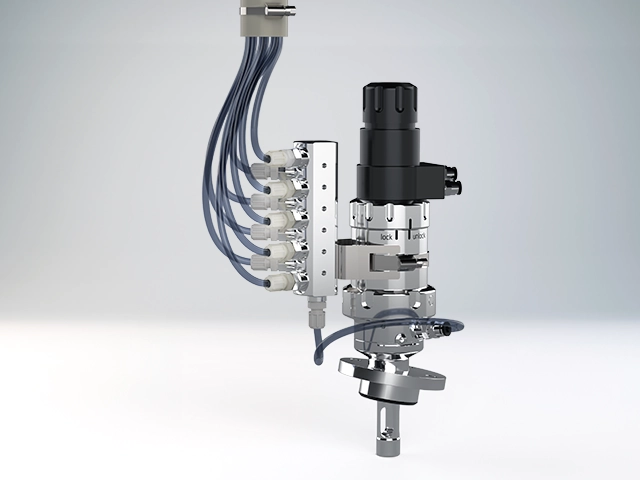
Media collector
SIP-capable media supply to SensoGate retractable fitting.
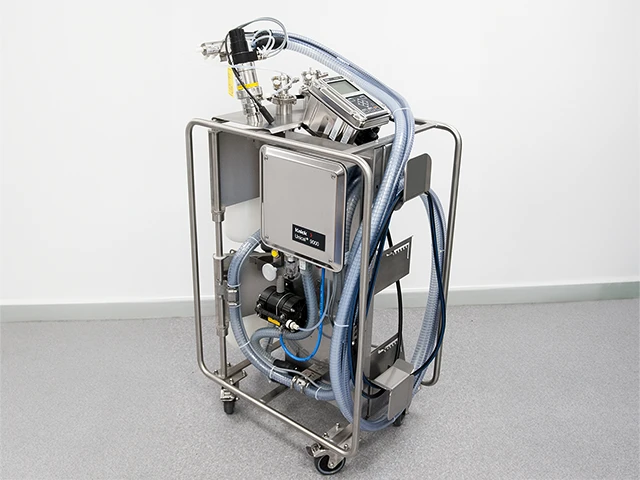
cCare pHarma mobile – Full cCare functionality on wheels
Where a permanently installation of the measuring system is not required or not feasible, for temporary use, e.g. in batch reactors without continuous operation, or for comparative measurements, this flexible special solution with full audit trail functionality including access control can also be used.
Audit trail and remote login - documentation and safety
Modules are available for the Protos II transmitter to meet the requirements of the pharmaceutical industry, in which all process interventions must be recorded and documented in an unalterable form in accordance with 21 CFR Part 11 of the FDA.
Every change to the measuring point must be provided with a time stamp and user information. Transmitters in the production plant are usually locked and must be unlocked by entering a passcode. However, the process control system does not record who has made which change at the measuring point.
With the Protos II transmitter, Audit Trail can be implemented via remote login directly via the customer's process control system. After authentication (e.g. via RFID), the transmitter of a specific measuring point can be unlocked by 2-factor authentication, either by a generated code that must be entered at the transmitter or by a personal release. This measuring point release only takes place with the rights that are defined for the respective user.
Logging in and out as well as all changes to the transmitter, e.g. in parameterization, configuration or replacement of a sensor, are recorded directly and automatically documented in the audit trail.
This data is transmitted directly to the process control system without gaps, unchangeable and assigned to each measuring point.
The audit trail functionality is currently implemented via PROFIBUS PA, other protocols such as PROFINET (also in the Ex-capable APL version) will follow.
More information needed? We look forward to hearing from you!
Contact Us
Overview of specific applications and product solutions in various fields of BioPharma.