프로세스 분석
Plant Utilities: Optimization of Liquids Analysis
Various plant utilities such as water treatment, steam generation, cooling, and heat recovery serve the production plants in the process industry.
To support the production process, the plant utilities must operate smoothly. Water supply or steam generation failures force the main processes to shut down, resulting in significant costs.
In plant utilities, various chemicals are added to the water to prevent biological growth and to neutralize corrosive substances. Depending on the application, pH, oxidation-reduction potential (ORP), conductivity and dissolved oxygen must be measured to support dosing and process control.
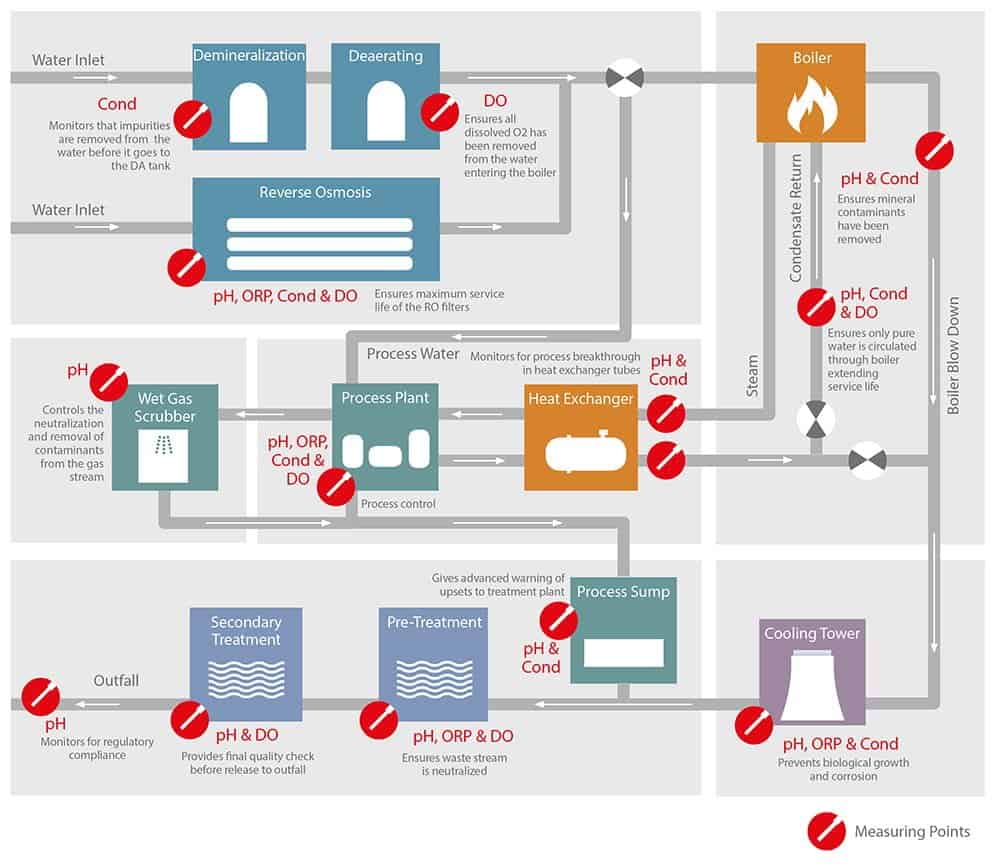
Protecting Industrial Plant Utilities against Corrosion, Deposits and Wear
In industrial processing plants such as oil refineries and pharmaceutical or chemical factories, many utility plants provide and extract the auxiliary media required by the main process. Water – derived from pure or ultrapure water – is almost always used and steam must be generated for cleaning and sterilization. Treating the wastewater produced is also a complex process.
The water that will be used in the process must first be filtered and disinfected in reverse osmosis systems. To precisely control the osmosis processes, the degree of water contamination and rejection must be determined via conductivity measurement. The correct dose of germ-killing chlorine to be added is based on ORP measurement. The pH value determines whether or not limescale on the osmosis membranes makes it necessary to replace them.
If the water will not be used in the process but instead to generate steam, all of its mineral components must be removed in a full demineralization unit and the dissolved oxygen must be removed in degassing units before it can enter the steam generator. These processes are controlled accordingly by measuring conductivity or dissolved oxygen.
Steam generation, heat dissipation and recovery
The condensate from heat exchangers or cooling towers is returned to the steam generator circuit. To reliably protect the heating pipes in the steam generator, the pH, conductivity, and oxygen in the condensate must also be measured. Adding sodium phosphate and sodium hydroxide makes the water more alkaline to prevent corrosion. Other additives such as hydrazine bind oxygen and also minimize corrosion. To prevent overdosing, which can also lead to problems, the appropriate dosage is controlled by pH and dissolved oxygen measurements.
Steam that has already been used to sterilize plant components still contains plenty of thermal energy, which can be recovered in heat exchangers and provided to other processes.
Pipes are the most critical parts of heat exchangers, since leakage caused by corrosion can lead to contamination and significant plant damage. When steam is cooled down in an intact plant, it precipitates as pure condensate. Therefore, increased conductivity of the condensate is an indication of corrosion caused by contamination or process breakthrough.
Process heat from the cooling circuits that is not needed is dissipated through cooling towers. In order to prevent mineral deposits there, the water’s pH value is controlled by adding acid. Adding oxidants ensures disinfection and prevents organic growth in the pipes. The required dose is determined by measuring the ORP.
Wastewater neutralization
Before wastewater can be fed into the public sewer system, it must be treated until its pH, dissolved oxygen, and ORP values are within the permitted range. Process water and wastewater from gas scrubbers are treated similarly.
Preventing measurement problems in moist environments
As a rule, the measuring points for industrial process plant utilities are exposed to very moist or wet environmental conditions under which conventional analog sensors do not function ideally. Moisture, corrosion and deposits on metal connector contacts can lead to drift or distortion of the measured values. However, the alternative, which is using dedicated analog sensors, increases maintenance effort because the cables must be removed from the transmitters and the cables of the replacement sensors must be laid.
Digital Memosens sensors are the perfect solution, as their contactless connectors are completely resistant to moisture and contamination of all types. Energy and measured values are transmitted via inductive transmission, thus eliminating distortion due to insufficient contact. Memosens sensors improve pH, ORP, oxygen and conductivity measurements in plant utilities.
Return on Investment
- Memosens technology with perfect galvanic isolation eliminates the typical contact problems and measured value distortion that plague conventional analog sensors in moist or wet environments.
- The high reliability and accuracy of the measurements enables perfect chemical dosing. This prevents inefficient overdosing, improves process quality and increases the service life of utility plant systems.
- Precise conductivity measurement enables the early detection and elimination of corrosion and leaks before they lead to expensive damage to plants and the environment.
- The time required for sensor replacement is reduced to a minimum with Memosens. Since Memosens sensors can be pre-calibrated in the laboratory, complex, unsafe, and expensive on-site pre-calibration under difficult conditions is a thing of the past.