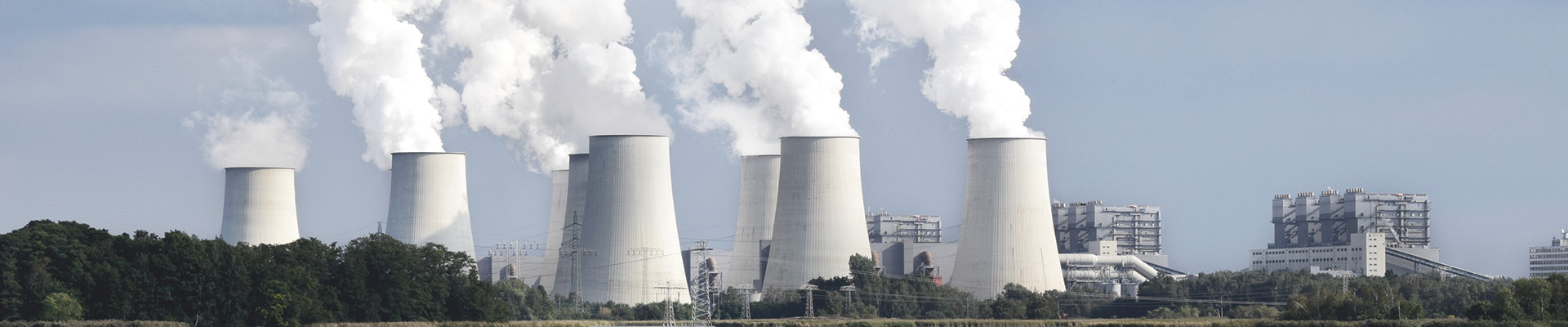
PROCESS ANALYTICS
Cooling Tower Monitoring
Cooling Tower Monitoring
In a wide range of industrial sectors, cooling towers are used to dissipate process heat from cooling circuits.
Mineral deposits and corrosion reduce their efficiency and lead to premature wear on plant parts. Further, lime or corrosion deposits offer a platform for organic material and biofilm. As a result, colonization by Legionella bacteria can lead to the contamination of plant parts and serious health hazards, for example. In order to avoid unplanned downtime, the expensive plants must be carefully maintained.
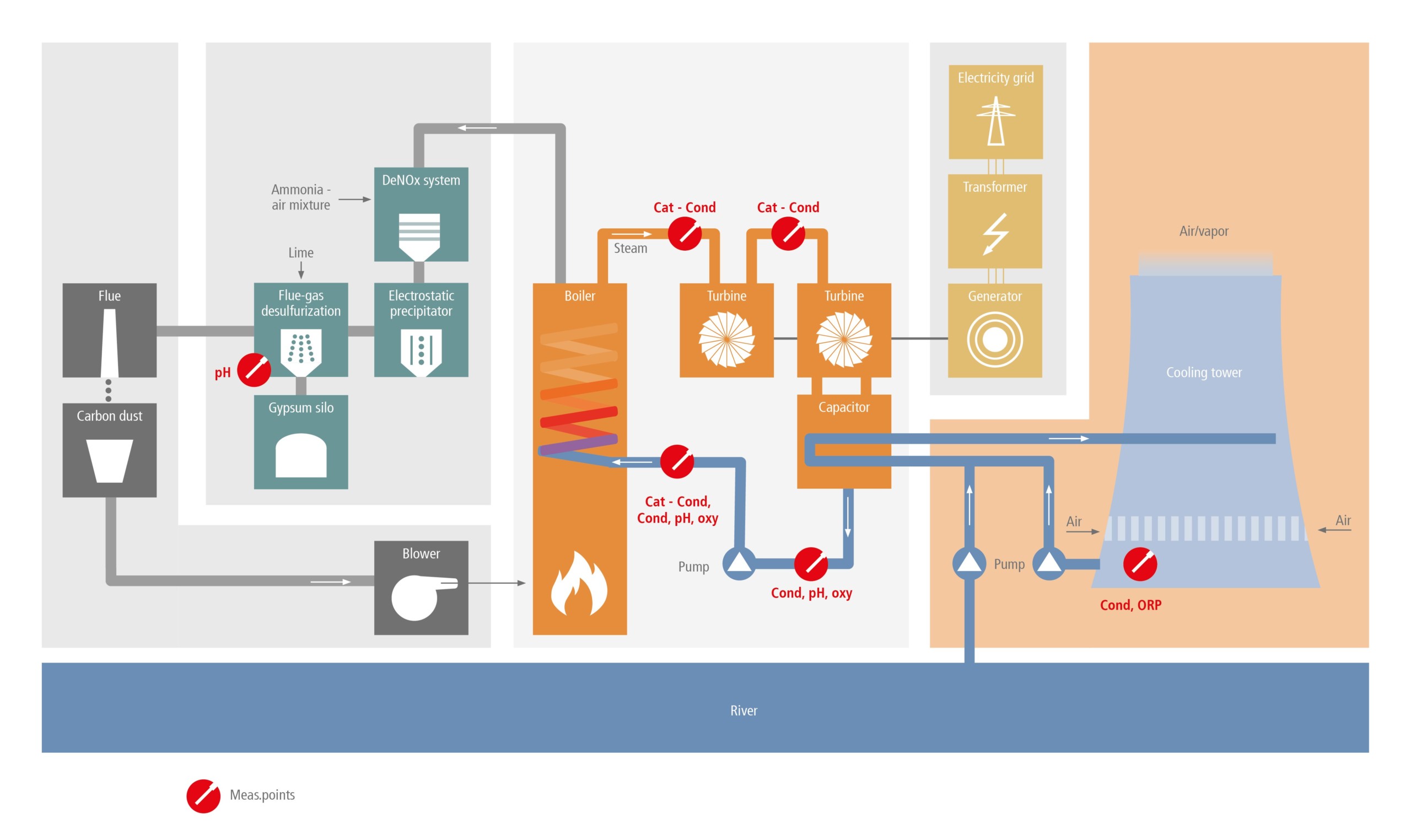
Reliable Process Measurements Prevent Downtime
In order to prevent mineral incrustations on plant parts, the pH value of the water in cooling towers is regulated by the addition of acids like sulfuric acid. They neutralize or dissolve the alkaline calcium carbonate in the cooling water to prevent lime deposits, which have a negative effect on heat exchange and therefore, the efficiency of the cooling plant. Monitoring pH regulation with digital Memosens sensors like SE555 minimizes corrosive effects and enables process breakthroughs to be detected early on.
Metering equipment feeds oxidizing agents in a controlled manner into cooling towers in order to disinfect the water and pipe surfaces. The concentration of the oxidizing agent (typically sodium hypochlorite) in the water is monitored by using ORP sensors to measure the oxidation/redox potential. The quantity of oxidizing agent required to completely disinfect the cooling tower is based on the measurement. The Memosens SE565 ORP sensor featuring measurements with high precision and repeat accuracy is used for these processes. It is designed for hygienic processes and sterile applications.
The purpose of desalination is to reduce the salt content in the cooling system by removing minerally enriched cooling water and supplying water with a minimum salt content to the system. This is why automated desalination requires conductivity measurements that provide information about the salt content of the water.
The Memosens SE630 sensor made of non-corrosive material measures contacting conductivity up to 20 mS/cm. The robust design of the sensor ensures a long service life – even in high pressure and temperature ranges.
Since the connections of conventional analog sensors are usually not watertight, using them in moist environments like cooling towers is a challenge. This is why manufacturers of analog products encapsulate the connecting cable in the sensor – with the consequence that users must remove the cable at the transmitter during sensor replacement.
Thanks to their contact-free, fully moisture-proof transmission of measured values, these circumstances are eliminatedwith Memosens sensors. Because the sensor coupling inductively transmits data between the sensor and the cable, these sensors can also be plugged in under water.
Memosens technology makes it possible to pre-calibrate the sensors under ideal conditions in the laboratory and then have them replaced on site – even by untrained personnel. Memosens couplings are available for pH/ORP, dissolved oxygen, and contacting conductivity sensors. Knick recommends using the industrial transmitters in the Stratos series.
Return on Investment
- Use Memosens technology to reduce the time and money you spend on maintaining and repairing your measuring loops: By using the Memosens SE555, SE565 and SE630 sensors and transmitters in the Stratos series, you significantly reduce the frequency of necessary calibration and sensor replacements – and with this, the number of sensors that you hold in reserve. At the same time, simplified maintenance reduces personnel costs.
- Automated monitoring and regulation of the chemical sequences in the cooling circuit not only reduces cost-intensive corrosion damage, but also reduces the amount of water and chemicals required for maintenance. As a result, the entire plant has a longer service life.