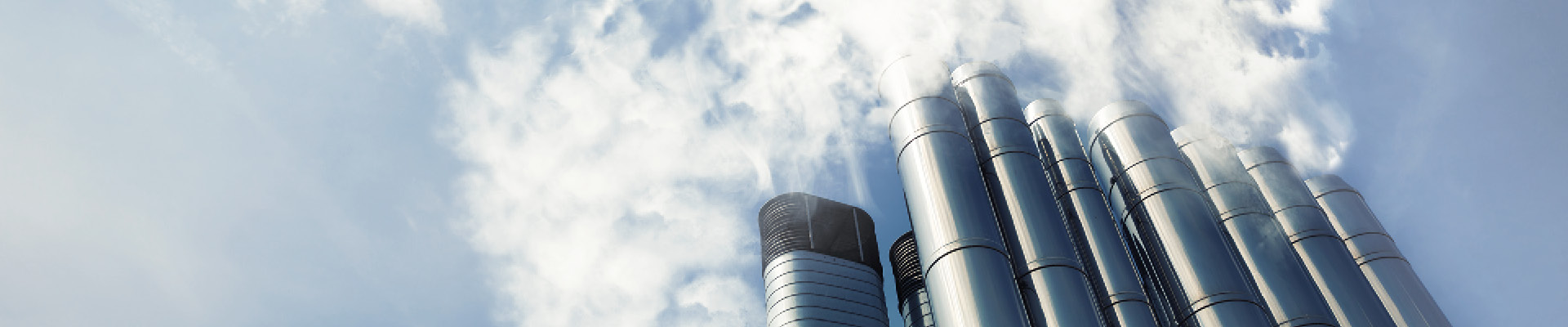
PROCESS ANALYTICS
Flue Gas Desulfurization
Flue Gas Desulfurization
In the wet scrubber, the corrosive SO2 gas from the exhaust flue gases of fossil-fuel power plants or incineration plants is removed. Limestone powder, burnt lime, or calcium hydroxide are used to absorb SO2. Gypsum, which can be reused in the building materials industry, is the result. Accurate pH measurement is indispensable in this process in order to completely remove the SO2 and fulfill the official regulations for clean air.
Key Facts About the Application
Sector
Power plants with flue gas absorbers
Application
3 applications (1. Verifying the pH value in the pre-scrubber, 2. Neutralization, 3. Lime scrubber)
Measuring Parameter
pH
Main Requirements
The measuring loops are corrosive and thick incrustations form.
Measurement in Processes that Build Up Thick Gypsum Layers
Description of application
Application 1:
In the pre-scrubber (stage 1) the hot flue gas is cooled by bringing it into contact with lime slurry. The pH value is only slightly increased (normally between pH 1 and 2 at 80 °C). Here, the pH value must not rise above 2, since only HCl/HF and heavy metals must be precipitated. The SO2 is not bonded until stage 2. Precise pH control is crucial.
Application 2:
In stage 2, the main scrubber, the pH value is increased by adding more lime. SO2 is bonded. The addition of lime slurry must be controlled by constant pH measurement. If the pH values are too high, too much lime was added (higher costs) and the gypsum is contaminated by excessive calcium hydroxide. If the pH values are too low, the SO2 bond is less efficient.
The optimal pH value is between 5.5 and 6.0. Higher values lead to soft, greasy calcium sulfite deposits (soft plugging) and slightly reduced efficiency. Lower pH values lead to thick incrustations that are not easy to remove (formation of hard scale). In general, the pH measuring loop is in the backflow circulation line of the calcium sulfite/gypsum slurry.
Application 3:
The surplus water that remains after the precipitation/thickening of the gypsum must undergo a neutralization process. Sulfuric acid is added to bond the excess lime. Further, thick incrustations and deposits occur at this measuring loop.
All three measuring loops are extremely important for optimal process conditions. The points are corrosive and thick incrustations that necessitate a high maintenance effort are formed. Knick recommends fully automated cleaning and calibration systems for these applications in order to reduce manual effort and increase process reliability
Requirements of the application
The major challenge of this application is to build up thick layers of gypsum in the gas scrubbers.
Why Knick?
Due to its unique ceramic seal, Ceramat is the only fitting that is worth considering here. The deposit remover (pump sock) for Ceramat removes deposits that would otherwise completely clog the system. The unique sensor maintenance system cleans and calibrates the sensors fully automatically and reduces maintenance effort many times over.
Associated Products
Associated Industries and Applications
Overview of specific applications and product solutions in different areas of power plants.