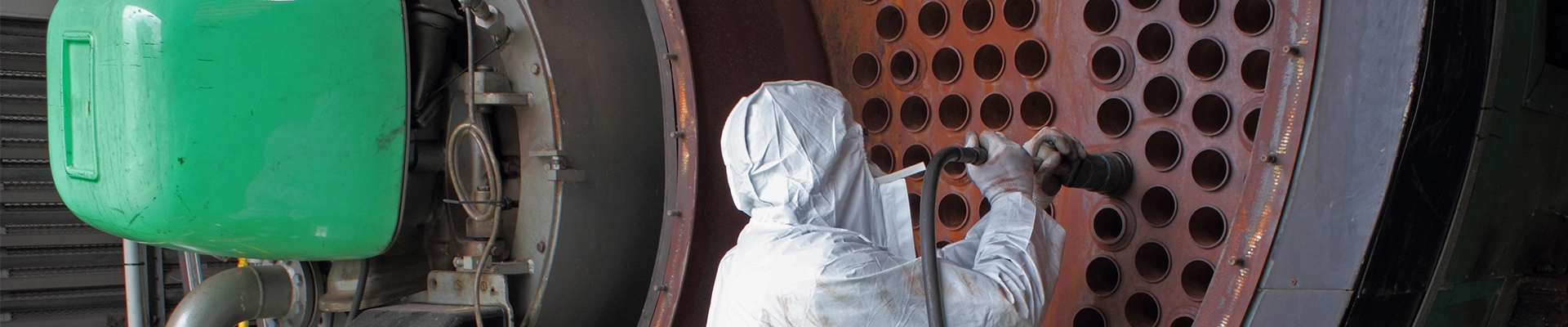
PROCESS ANALYTICS
Monitoring Steam Generators
Monitoring Steam Generators
Steam generators play a central role in a variety of processes. They feed generators or turbines in power generation, drive steam engines, provide power in thermal power plants, and are used in heat-consuming processes in the chemical and metal industries.
Since steam generators fulfill application-critical functions and the cost of their downtime or replacement is extremely high, damage caused by wear should be prevented by monitoring water quality. The following risks threaten the plant:
- Contamination of pipes with biological or mineral substances that negatively affect the efficiency of the plant
- Corrosion of plant parts, which shortens their service life and poses a potential hazard for personnel
- Inadequate monitoring of the condensate, which leads to an increase in the number of desalination processes and in turn, to the economically inefficient consumption of water, chemicals, and energy.
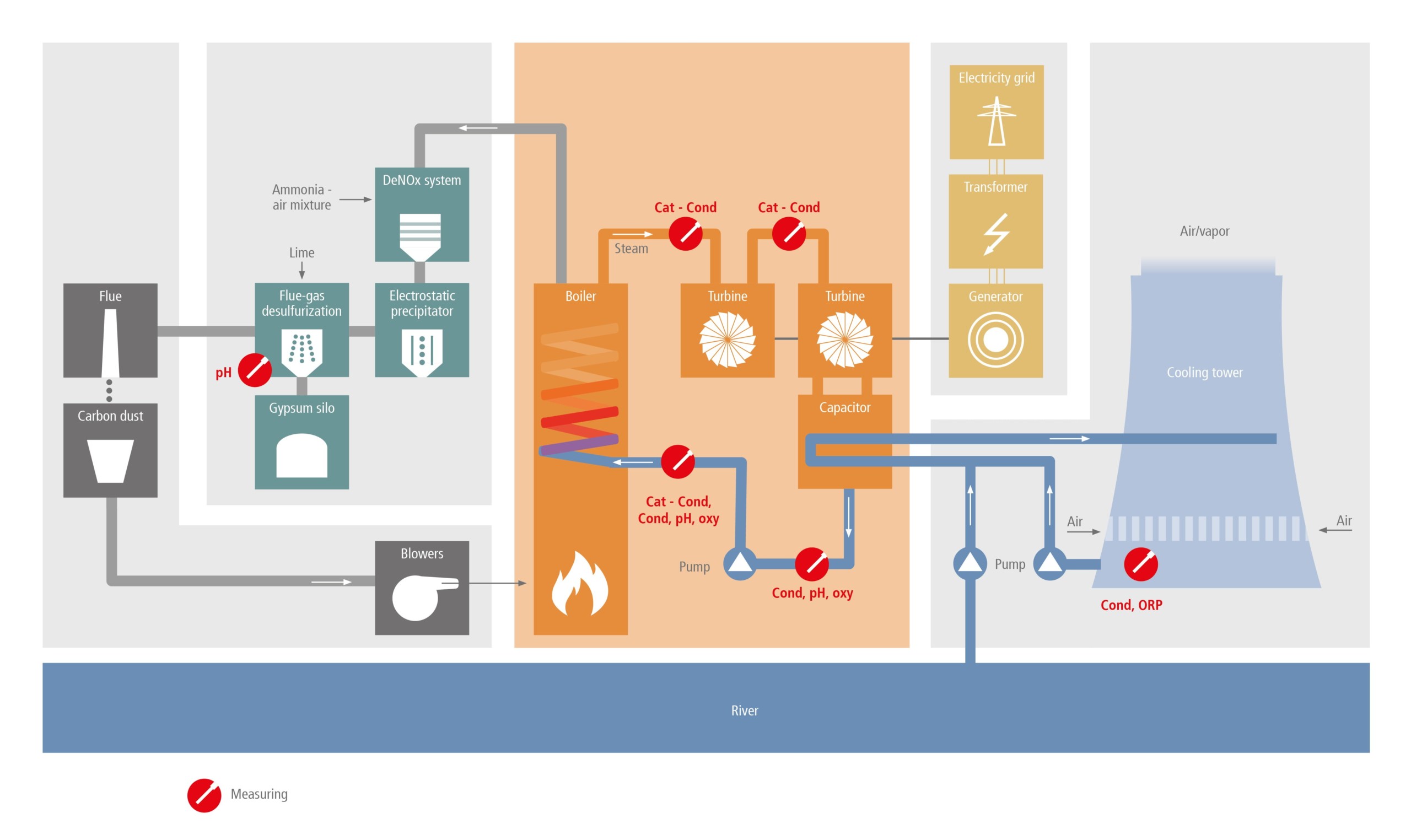
Monitoring Water Quality Ensures the Output of Steam Generators
Heating pipes are in special focus when it comes to steam generators. Normally, steam generators are supplied with alkaline water that provides favorable conditions for the formation of a thin oxide coating on the surface of the heating pipes to protect against corrosion. To alkalize the water, sodium phosphate and sodium hydroxide are added to it. However, excessive addition of these chemicals can lead to problems and their metering should be based on precisely monitoring pH measurement.
The SE558 sensor was developed by Knick for high-precision pH measurement in liquids with very low ionic activity, which is why it is typically used in ultra-pure water applications and water treatment for power generation.
With its highly corrosive properties – even the smallest concentrations in the ppm range attack metallic surfaces – oxygen has a significant influence on the service life of steam generators. For this reason, chemicals like hydrazine are used to bind oxygen radicals.
The SE707 sensor measures dissolved oxygen down to the detection limit range in traces of 1 ppb, enabling hydrazine to be properly metered. Defective heating pipes or overdosing chemicals can lead to harmful substance concentrations in the water that can be detected by measuring contacting conductivity.
An increase in conductivity indicates increased contamination of the water, which must be countered with desalination or, if necessary, a plant inspection. For the precise, reliable measurement of small and the smallest conductivity levels in pure water, cooling water, and boiler feed water, as well as in steam circuits, Knick developed the Memosens SE604 sensor with robust stainless steel electrodes in a coaxial arrangement. Like all Memosens sensors, SE604 has an integrated temperature detector for exact temperature compensation.
Since the connections of conventional, analog sensors are not watertight, manufacturers of analog products encapsulate the cable in the sensor. This is why users must remove the cable at the transmitter when replacing sensors. With the contact-free, fully moisture-resistant measurement transmission of Memosens sensors, this effort is a thing of the past. Thanks to inductive measured value transmission in the Memosens sensor coupling, neither moisture nor incrustation can have a negative effect on transmission.
Further, digital Memosens technology makes it possible to pre-calibrate the sensors under ideal conditions in the laboratory and then have them replaced on site – even by untrained personnel. The cell constants are automatically transmitted to the transducer and are available for additional calibration operations.
Return on Investment
- Since Memosens sensors need to be re-calibrated or replaced less often, your costs for measuring loop maintenance and procuring new sensors are significantly reduced.
- And for applications with a high volume of moisture in particular, you benefit from much simpler sensor handling. With the inductive data transmission and supply voltage characteristic of Memosens sensors, and thanks to the high degree of protection of the transmitters, you no longer need to worry about wet or corroded contact loops or damage to the electronics. The transmitters have a three-year warranty from Knick.
Associated Products
Associated Industries and Applications
Overview of specific applications and product solutions in different areas of power plants.